Introducing SPiRe®+
PATENT PENDING
Get expert guidance and a free quote for our seawall repair system. Maintenance-free service life and can be installed within weeks.
Introducing the Game-Changing Sustainable SPiRe®+
Following the successful launch of the Sheet Pile Repair (SPiRe®) system 5 years ago (in 2018), SPiRe®+ is our latest patent-pending solution whose applications are only limited to one’s imagination. This is a truly sustainable product that not only offers an infinitely long maintenance-free service life, but it also offers huge time and cost savings during the construction and installation phase of the project.
These panels are made with high-strength non-corroding Fiber Reinforced Polymer (FRP) and are installed as easily as the original SPiRe® system. The panels are 3-ft (914mm) wide and are available in 12-ft (3.66m) and 18-ft (5.49m) lengths; other lengths can be special ordered for each project. The wall thickness is 0.20 in. (5mm). The panels weigh 3.2 pounds per square foot (15.5 kg/m2). The panels are flat on one face and have protruding T profiles on the other face.
Advantages of the SPiRe+ for Seawall Repairs
The repair system presented here offers significant advantages over conventional repair methods. While the benefits may vary from project to project, some of the key benefits of this system include:
Here are some of the benefits of the new disruptive SPiRe®+ that encompasses so many features into a single product:
- It can serve as a rigid stay-in place form
- The unique T profiles physically grab and interlock into concrete, making the panel to act as an integral part of the wall or slab system
- The grit-coated side bonds perfectly to concrete, allowing the flat portion and the T profiles to act as the reinforcing elements for the concrete
- It is a reinforcing element equivalent to #5 Gr. 60 bars at a spacing of 2.5 in. (15mm, 400MPa bars at 60mm); this is far more tension capacity than what most walls or slabs require thus the panel eliminates the need for all reinforcing bars!
- The panel and the T profiles are non-corroding, providing a long maintenance-free service life
- The panels are waterproof and eliminate the need for waterproofing on retaining walls
- The impervious panels keep water and oxygen away from the host structure, significantly reducing the corrosion rate
- SPiRe®+ panels can be installed underwater without the need for any coffer dams
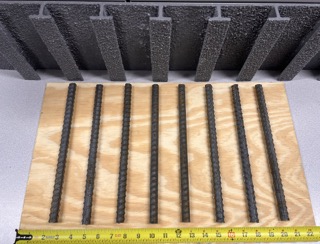
Applications of SPiRe®+
The new SPiRe®+ panels have many applications where significant cost and time savings can be recognized. A few of these applications are listed here and explained in more detail below:
- Repair of seawalls and bulkheads over the splash zone region without coffer dams
- Extension of seawall elevations to protect communities from rising sea levels and flooding caused by climate changes
- Repair of severely corroded seawalls and bulkheads by horizontally spanning the panels between new or existing piles
- Repair and strengthening of corrosion-damaged decks in jetties and piers
- Repair and strengthening of beams in bridges (& buildings) with minimal service disruption
- Construction of new retaining walls including waterproofing
- Construction of noise-barrier walls along freeways
Seawalls & Bulkheads (Splash Zone Repair)
If corrosion damage is concentrated around the splash zone (defined as the elevation between low and high water marks) on the bulkhead or seawall, it is possible to repair the damaged zone only. In this case, the height of the SPiRe®+ panels must extend a couple of feet above and below the corroded region. You can download our typical design details here. L-bolts are anchored to the existing seawall on an approximate 3-ft x 3-ft (1m x 1m) grid. The SPiRe®+ panels are connected to these bolts and adjusted to provide the required stand-off distance from the wall. The overlapping edges of the panels are sealed with a rubber butyl sealant to make them watertight. This process is continued until you cover the length and height of the seawall that requires to be repaired, creating an annular space between the SPiRe®+ panels and the host structure.
At this time, the bottom and sides of the annular space must be sealed. There are many ways to do this. One technique is to pass threaded eyebolts through the bottom row of those L bolts, allowing them to hang vertically and extend a few inches below the repair height. Flat plates about 18-in. (400mm) wide X several feet long made with FRP or plywood can be cut along one edge to match the profile of the existing seawall. The other “straight” edge will sit below the bottom of the SPiRe®+ panels. These plates will be pushed upward and held tightly in place by those eye bolts. We recommend to place an epoxy grout at the bottom and the top of the cementitious grout in the annular space. This is intended to seal the cementitious grout against any water and moisture intrusion. The epoxy grout is placed at the bottom and it will flow to cover all holes and openings and to create a seal at the bottom of the annular space. Then the bulk of the annular space is filled with cementitious grout; the grout specifications are also available for your use. The tremie method could be used for placement of the grout. Finally, the top of the annular space is filed with epoxy grout.
In some projects the top and/or bottom of the SPiRe®+ panels can also be anchored to the soil. It may be required to provide a new beam along the top and bottom of these panels to transfer those loads and reactions into the soil or a dead man.
The repair technique discussed here offers significant advantages, including the following:
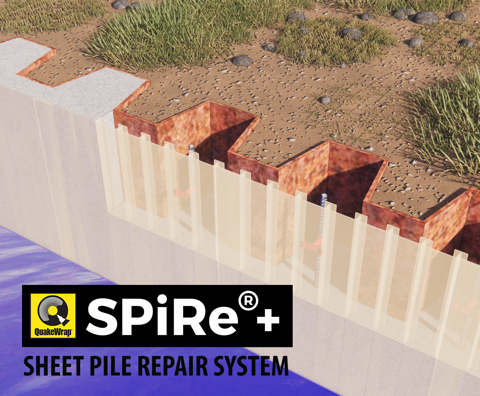
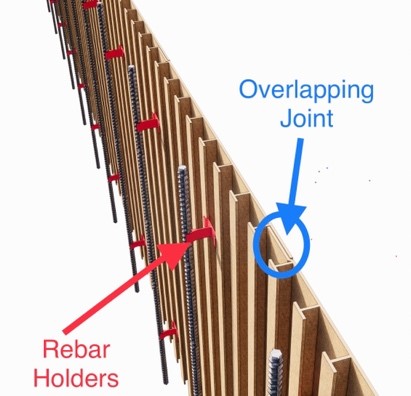
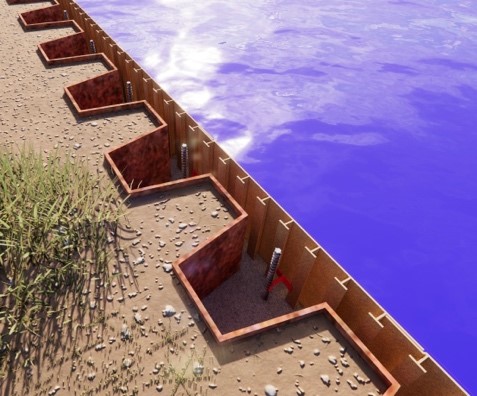
Repair of Severely Corroded Seawalls
When the original sheet pile is severely corroded, new steel H piles can be driven a few inches away from the seawall and the SPiRe®+ panels are placed horizontally, spanning between the existing or newly-driven H piles. The new system can be designed to resist all or part of the soil pressure that was being taken by the corroded seawall. Care must be taken to protect the new steel H piles from future corrosion. However, the SPiRe®+ panels offer a very long maintenance-free service life and they will not corrode.
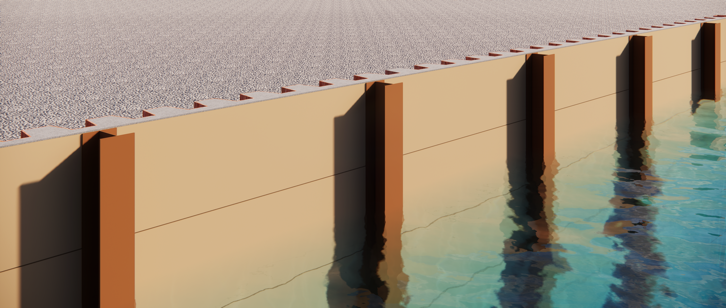
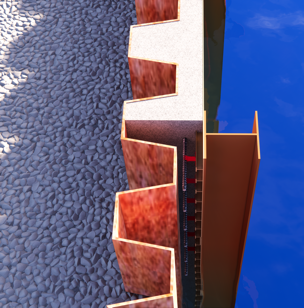
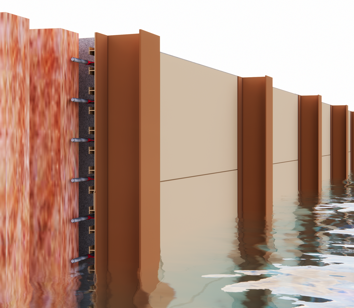
Repair of Beams and Decks in Ports
In many ports and piers, the beams and the deck are very close to the water. This not only causes significant corrosion in the beams and deck, but it also makes the repairs very challenging. The limited space between the beams and deck and the high water elevation makes it difficult to use any cranes for lifting the repair materials under the deck. Conventional repair techniques, for example, that require the use of plywood or timber to build a form around the deteriorated beams and deck become very heavy to handle and add significant time and cost to such projects. More importantly, after the repairs are complete, the timber formwork must be removed. This, not only adds to the project cost, but the beams and deck will become exposed to the seawater and will soon begin to corrode similar to the original construction.
The patent-pending SPiRe®+ panels provide major cost and time savings in such projects. For repair of a deteriorated beam, for example, the panels can be cut to the required width and length in advance and their edges can be bonded using L-shaped angles, epoxies and bolts. These panels can be transported on barges to the underside of the deck. The beam surface needs minimal preparation or patching of the damaged areas; in fact, an uneven and rough surface is preferred over a smoothly finished one. The entire repair assembly can be lifted quickly and secured to the underside of the deck or slab with anchor bolts. The annular space between the SPiRe®+ panels and the beam is filled with non-shrink grout or concrete. The entire operation may be completed very quickly with minimal disruption to the marine traffic. Once the repair is completed, the SPiRe+ panels will permanently remain in place, protecting the host pier from exposure to seawater and corrosion.
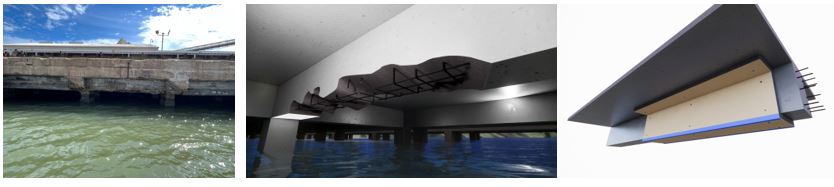
Repair of Bridge Girders and Beams
Conventional repair of bridge girders is very time consuming and often requires disruption of traffic. The SPiRe®+ panels provide major cost and time saving in such projects. For repair of a deteriorated bridge beam, for example, the panels can be cut to the required width and length and their edges can be bonded using L-shaped angles, epoxies and bolts. The beam surface needs minimal preparation or patching of the damaged areas; in fact, an uneven and rough surface is preferred over a smoothly finished one. The entire repair assembly can be lifted quickly and secured to the underside of the bridge or slab with anchor bolts. The annular space between the SPiRe®+ panels and the beam is filled with non-shrink grout or concrete. The entire operation may be completed in one night when the traffic on the roadway is light.
Construction of New Retaining Walls
For construction of a retaining walls, the concrete footing must be first constructed. 90-degree Starter bars are positioned in the footing and they will extend out vertically by about 2 feet (600mm). Then the SPiRe®+ panels are placed on top of the footing and connected together using sealants at the overlapping joints to make the panels watertight. Similarly SPiRe®+ panels are placed on the opposite side of the wall at a distance equal to the desired retaining wall thickness (minimum of 4 inches or 100mm). These panels are connected together with a few through bolts. The SPiRe®+ panels are temporarily braced while concrete is placed between the two sets of panels.
The SPiRe®+ panels serve as the reinforcing elements for the wall; the overlap length of the starter bars is sufficient to transfer the load from the SPiRe®+ to the foundation. The advantages of this system include:
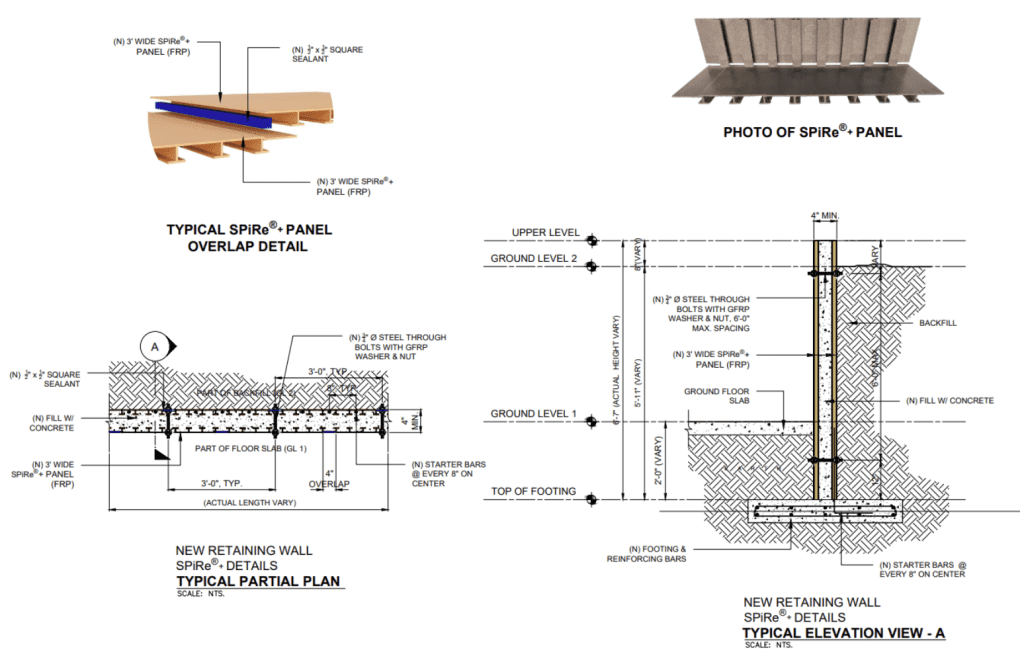
Test Results
An 8-inch wide x 9-ft long (200mm X 2740mm) piece of SPiRe®+ was used as a form to cast a 4-inch (100mm) tall beam. Quikrete non-shrink Precision Grout was used instead of concrete. The specimen was allowed to cure for 6 days before it was tested as shown in the photos. We had to stop the test at a load of 9190 pounds (40.9 kN) due to distortion in the testing frame.
The applied moment at this time to the 8-in. (200mm) wide beam was:
(9190/1000) * 24” = 220.6 k-in. or 330 k-in. (24.9 kNm)
The test proves that the internal grit-coated surface of the panel allowed full engagement of the panel. The T profiles and the flat panel acted as reinforcing elements as assumed. The contribution of the panel is more than #5 Grade 60 steel at 2½ in. o.c. (15mm diameter 400MPa steel bars at 60mm spacing). This is a tremendous achievement considering how easy it is to assemble these panels and the long service life and corrosion protection that the SPiRe®+ panels provide.
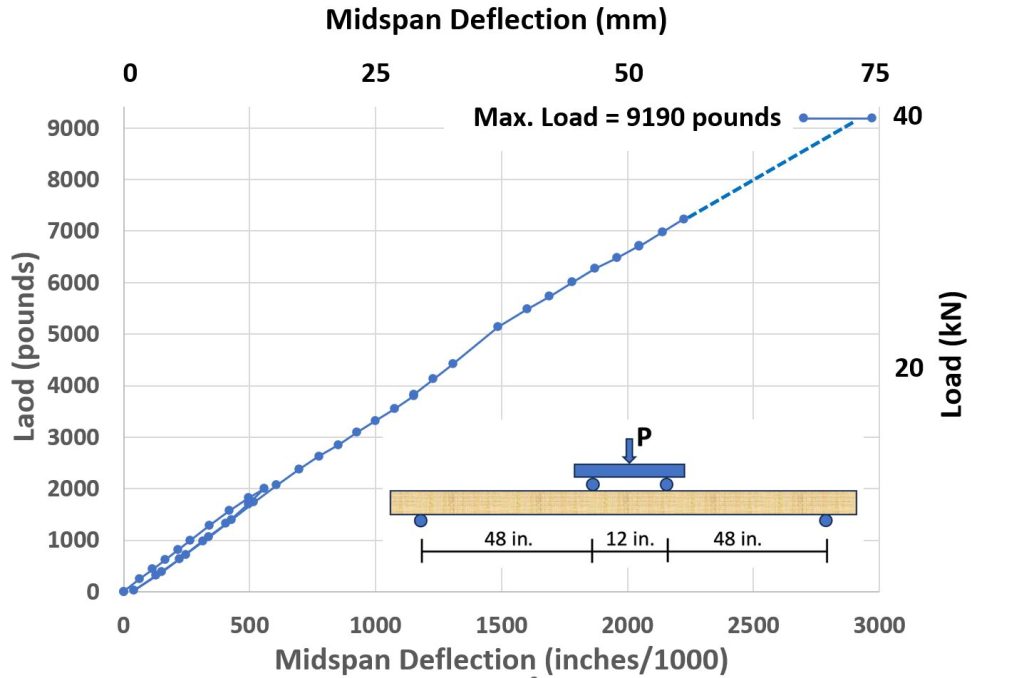
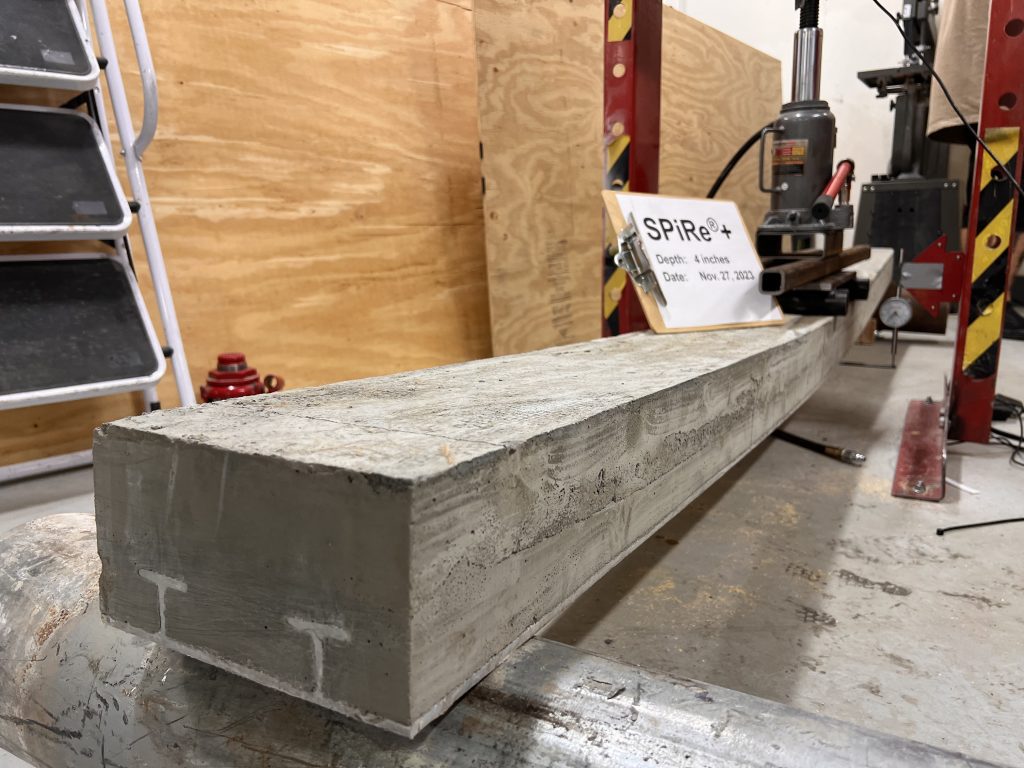
Papers, Case Studies & Projects
Click here to download a paper that describes the evolution and many uses of SPiRe+ (Download Paper).
Note: The project below showcases the use of the original SPiRe® system for repair of a deck in Galveston, Texas. Another video shows the use of SPiRe®+ in repair of a timber seawall in New York. As additional videos for repair of slabs and beam become available, they will be posted here.