Piles and Piling
Get expert guidance and a free quote for our pile repair system. Maintenance-free service life and can be installed within weeks.
Piles
The dry-wet cycle in marine environment leads to rapid corrosion of submerged piles. This is particularly significant around the splash zone. If you are wondering how to repair or strengthen a corroded submerged pile, whether it is made of timber, concrete or steel, we invite you to download our specifications and typical details.
The Problems with Common Jackets
Conventional FRP jackets are typically made of two half shells that are connected in the field around the piling and filled with concrete or grout. There are several major problems with these products:
- The jackets must be custom ordered in advance for the size of piling being repaired; wrong sizes could delay the project.
- The jackets are bulky adding cost for shipping and storage
- The seams along the sides of the jacket let moisture and oxygen in, resulting in continued corrosion of the pile
- From an engineering point of view, these seams are the weakest point in the jacket and they do not offer any confinement for the pile and the concrete or grout
When the US army Corps of Engineers undertook a massive study to select the best piling repair system, they cited the above shortcomings in their report and decided to only complete the investigation with PileMedic.
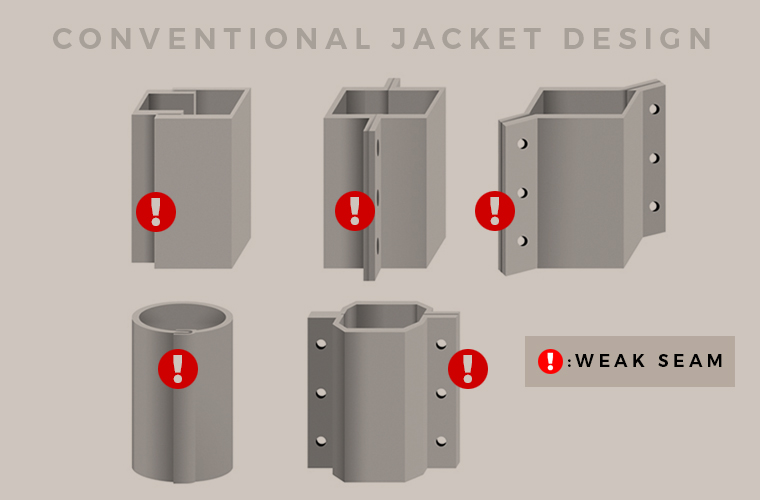
Advantages of PileMedic®
Looking for Help with your Project?
Schedule a Call
Get free advice for any upcoming projects or repairs
See Specs and Sample Designs
Get full specs and details to plan out your next project
Timber, Concrete or Steel Piling
The procedure for repair and strengthening of piles (pilings) is virtually the same regardless of the materials of the original pile. The only exception is for load transfer in steel piles as explained below using ShearWrap and ShearClamp.
When strengthening is required, we create a new ring of reinforced concrete shell around the existing piling. These shells will be built using non-corroding Glass Fiber Reinforced Polymer (GFRP) Rebars that ensure long service life for the repaired pile. With this approach, the new concrete shell can be designed to have as much capacity as required, even to replace the 100% capacity of the pile if the original piling has 100% section loss!
The repair process begins by securing the required number of spacers around the pile at 2 to 3 feet on center. These spacers are typically 1 to 2.5 inches long to create a 1 to 2.5 inch thick annular space around the piling. If any reinforcing bars are required for strengthening of the pile, they will be snapped into the spacers. Four-feet wide PileMedic laminates are epoxy coated and wrapped around the pile to create a shell that is two-layers thick. Ratchet straps or zip-ties can be used to prevent th e unraveling of the jacket while the epoxy cures. Another 4-ft laminate an be similarly wrapped and overlapped with the previous ones by 4 inches. This process will be repeated as many times as required to create a jacket of desired height around the piling.
The bottom of the annular space must be sealed. This can be done by embedding the shell a few inches into the seabed. If the jacket does not extend to the seabed, ShearFlange or skirt pins can be used to create a seal at any elevation. Next, the annular space will be filled with grout or concrete using the tremie method or by pumping through the ports that we supply and can be inserted along th height of the jacket.
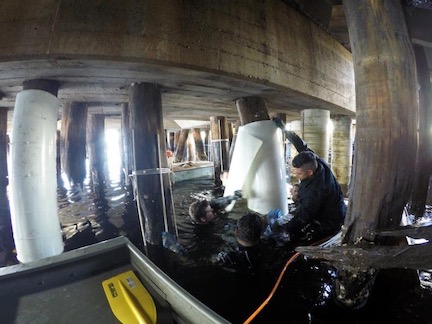
How Does FRP Reduce Corrosion Rate in Piles?
It is a well-recognized fact that oxygen and moisture are the fuel to the corrosion process. That is why we keep painting steel structures to keep moisture away from the steel. Unfortunately, after a few years, the paint cracks and flakes off and that leads to the corrosion of steel. The two independent studies cited below attest to the effectiveness of FRP in prolonging the service life of piles in marine environment.
In a 3-year study conducted by Texas DOT at the University of Houston, the researchers studied the effect of wrapping steel H piles in PileMedic on corrosion rate. As the authors mention on page 382 of this report, “…. in piles repaired with PileMedic, corrosion was not detected. Figures 10.42 and 10.43 show the repaired piles subjected to accelerated corrosion process in which no evidence of severe corrosion was observed.“
In another study at University of South Florida, researchers conducted tests on concrete piles wrapped in FRP and submerged in marine environment. Unfortunately, the FRP jacket was only extended 7 in. (175mm) beyond the corroded region. This is a short and insufficient length. In the same manner that you would not paint half of a steel beam and expect it to not to corrode, the FRP jackets should have extended farther beyond the already corroded zone in these specimens. In spite of this shortcoming, the authors conclude on page 79 of their paper that the average corrosion rate for wrapped specimens was only 30% of the unwrapped specimens.
In many of our designs, we take an even much more conservative approach and assume that all of the steel reinforcing bars (in the case of reinforced concrete piles) or the steel tube or H pile will corrode and vanish! Similarly, we can assume that timber piles will disintegrate with age. These are highly unlikely occurrences that lead to very conservative and safe designs. The repair systems we propose for such cases is a new concrete pile that surrounds the old pile; this new pile has no steel in it. Instead, it is reinforced with high-strength non-corroding GFRP rebars. Thus, there is no concern about the new pile corroding with age and losing its capacity. The new FRP-reinforced concrete pile can be designed to take all the loads independent of the host pile, thus eliminating any concern about how long the original pile will last.