IBC 18-10
KEYWORDS: Carbon Fiber Reinforced Polymer (CFRP); Repair; Strengthening; AASHTO girder; Damage
ABSTRACT: In its first application of Carbon FRP, ADOT successfully completed the repair of 12 AASHTO Type II girders that were damaged by truck collision. The loss of flexural strength in the girders varied from 20% to 50%. The positive outcome of this project will allow ADOT to include this repair option in future similar applications.
INTRODUCTION
This paper presents the repair of two bridges that were recently completed in Phoenix, Arizona. The bridges were along interstate 1-17 which is a major freeway passing through Phoenix. The project locations are shown in Fig. 1.
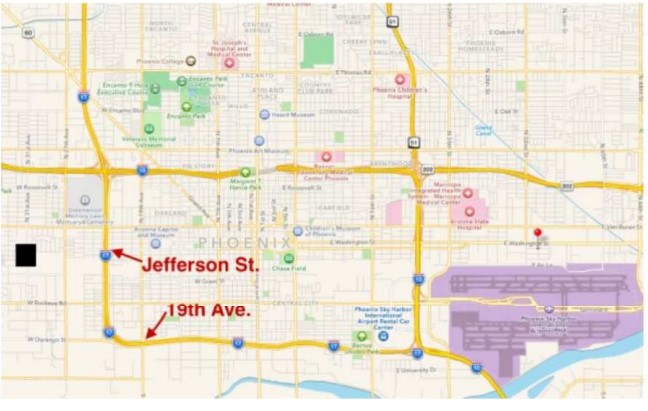
The first was an underpass, 1-17 at Jefferson St. The second was an overpass, 1-17 at 19th Ave. The bridges are located in downtown Phoenix Arizona and are less than 2 miles apart. During 2010, 1-17 in this area of Phoenix had only 3 lanes in each direction with an Annual Average Daily Traffic (AADT) volume of 100,000 with trucks comprising approximately 9.6% of that volume. Traffic disruptions in the bridge vicinity have always been a major concern.
The bridge at Jefferson Street is a two simple span precast prestressed AASHTO Type II concrete girder bridge built in 1959. The bridge is 132′-9″ long composed of two 65′-4 ½” spans with an out to out width of 64 feet. The existing northwest girder over 1-17 southbound has been repaired multiple times due to vehicle collisions in 2003, 2006, 2008 and 2014 (Fig. 2). Each time the girders were repaired and the girder shape reformed to the original shape. Several of the remaining girders have sustained minor damage consisting primarily of spalls, exposed rebar and minor cracking. Only the single northwest girder over 1-17 that was severely compromised was of concern at this time.
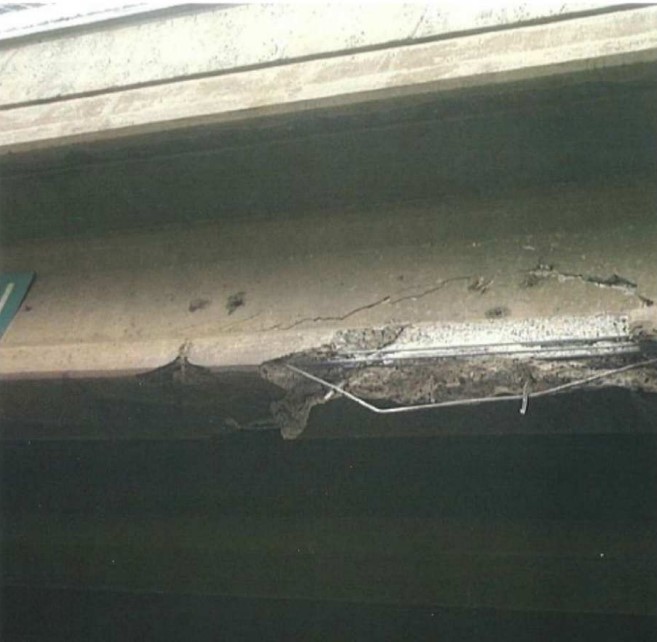
The bridge at 19th Ave was originally two two simple span precast prestressed AASHTO Type II girder bridges built in 1961. In 1984 the median between the two bridges was closed with four precast prestressed Bl-36 box beams to form a single structure. The current bridge is 103′-9″ long composed of two 49′-3″ spans with an out to out width varying from 122′-5″ to 125′-7″. The 19th Ave bridge has endured numerous vehicle collisions. Most of these collisions are minor collisions leading to spalling at the bottom flange of the girders. Several girders have had exposed rebar and few collisions have led to exposed and damaged prestressing strands.
Due to the vast numbers of collisions and the fact that it is very unusual to catch a vehicle that has impacted the bridge, it is impossible to determine exactly how many times this bridge has been hit. Moreover, it is difficult to determine if the damage was sustained from a single collision or multiple bridge collisions. Examples of several damaged girders can be seen in Fig. 3. Although the number of collisions to girders is greater at 19th Ave than at Jefferson Street, the amount of damage to any single girder is far less.
REPAIR ALTERNATIVES CONSIDERED
The Arizona Department of Transportation (ADOT) Bridge Group believed that with these collisions had most-likely resulted in a loss of strength in many of these girders. The determination of which girders needed to be strengthened was primarily based upon previous bridge inspections and records indicating which girders had prestressing strands damaged or exposed from a previous collision. Bridge Group believed any girders that did not have prestressing strands exposed did not have any significant loss in strength and could be repaired with concrete patching to protect from loss due to corrosion.
ADOT Bridge Group needed a way to restore the damaged girders to full strength without significant disruption to traffic in the area. Because of the heavy traffic volumes, girder replacement was not a viable option. 1-17 cannot be closed that long. Fiber Reinforced Polymer (FRP) was chosen primarily because it could be installed quickly and with minimal distribution to traffic. With the possibility of a girder replacement removed, FRP seemed to be the only choice.
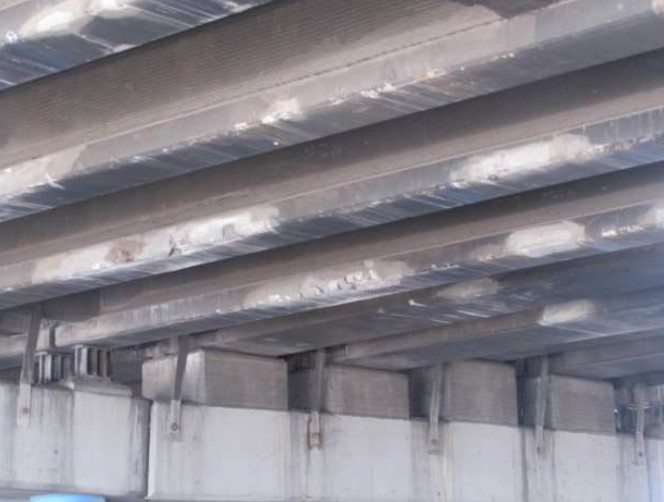
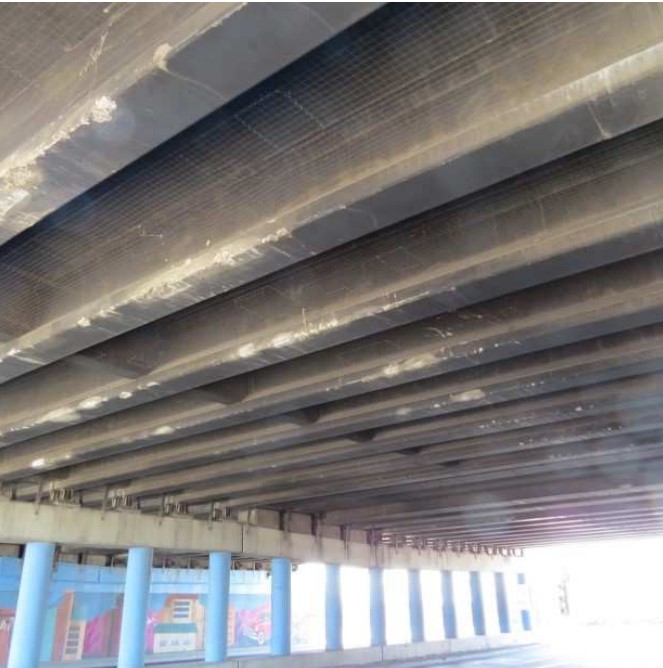
Strengthening of structures with FRP is a technique that was pioneered by the author in the late 1980s (Ehsani and Saadatmanesh 1990). In this technique, fabrics of arbor glass are saturated with epoxy and are externally bonded to the surface of the structural member. Within several hours, when the epoxy cures, the FRP reaches a tensile strength that is 304 times that of steel. The design guidelines by ACI and AASHTO require that the substrate be of a good quality and provide a minimum tensile strength of 200 psi. This requirement is easily satisfied for AASHTO girders that are manufactured in plants and with good quality concrete.
Each layer of FRP is typically around 0.04 to 0.05 in. thick. The fabrics are flexible during the installation phase and they conform to the shape of the girder. A further advantage of FRP is that it provides an impervious encasement for the structural member. In cases where the member is fully encased in FRP, this layer prevents the ingress of oxygen or moisture and results in substantial reduction of corrosion rate.
ADOT METHODOLOGY
Although other state DOTs had utilized FRP for strengthening of girders, the State of Arizona had never done so. An ADOT Bridge Group Engineer began the process of researching this technique could be implemented on this project. It was discovered that the City of Phoenix had performed a strengthening of bridge girders with Carbon fiber reinforced polymer (CFRP). With extensive research on the internet, contact with the bridge engineers at the City of Phoenix and discussions with CALTRANS, ADOT decided to proceed by using CFRP and had a method to perform the project.
Once the use of CFRP was selected as the method of repair, the next question was the extent of the repair for each girder. It was evident that the girders had lost strength due to impacts but without closing the bridges, attaching sensors and measuring results, an exact determination of the loss of strength was not possible. The original plan Record Drawings did not have complete strand data such as the number of strands and the strand placement information. This made it impossible to even determine the original design strength of the girders. Consequently, Bridge Group decided to base the full strength of the girder using the bridge load rating. After some calculation and using primarily engineering judgement a conservative value was assigned to each bridge on how much strength needed to be restored to bring the girders back to full strength.
The 1-17 underpass at Jefferson Street was determined to have a maximum flexural design capacity of 1988 k-ft. Since the girder at Jefferson Street had sustained multiple major impacts completely severing multiple strands Bridge Group assumed a strength loss of 50% for that girder. Thus, the FRP was supposed to provide an additional flexural capacity of 994 k-ft. It is noted that the girder on Jefferson Street was an edge girder supporting a sidewalk, not live traffic and the bridge was deemed capable of continuing to function even without that girder. At no time would ADOT risk public safety.
The 1-17 overpass at 19th Avenue Street was determined to have a maximum flexure moment design capacity of 1799 k-ft. Since the girders at 19th Avenue had only sustained minor impacts without completely severing strands, Bridge Group assumed a strength loss of 20%. Thus, the FRP solution was supposed to provide an additional flexural strength of 360 k-ft.
Bridge Group ran design calculation to verify that a CFRP design could be created that satisfied the strength requirements. Since federal money was used on this project ADOT could not choose a contractor or supplier for the work. The project had to go for an open bid. This gave Bridge Group one of its most difficult tasks, creating special provisions. Since the properties of CRFP vary between manufactures a performance based specification had to be created. This would give contractors and suppliers an equal opportunity to bid to work on the project. Because the CFRP material would vary based upon who won the bid Bridge Group could not design CFRP. Bridge Group could only call out the required performance. It was up to the contractor to provide the design that would meet the specified performance requirements.
As noted earlier, ADOT Bridge Group worked closely with CALTRANS in gathering information for Arizona’s first FRP project. Much of the work on the specifications came from specifications used by CALTRANS. ADOT Bridge Group adapted CALTANS specifications for use in Arizona, and eliminated several tests that were considered redundant. In addition, Bridge Group collaborated with the ADOT Materials Group and ADOTs internal testing labs to verify what tests Arizona wished to perform. The final decision was to secure the services of an outside independent testing firm for this project but require extra samples for the ADOT lab to test. ADOT testing labs wished to compare their results to the independent firm to verify if ADOT testing labs could perform the testing for future FRP projects.
The project was put out for an open bid. FNF Construction, Inc. was the lowest bidder and was awarded the contract. FNF Construction had chosen FRP Construction LLC (Tucson, AZ) as its FRP supplier and installer. FRP Construction LLC hired QuakeWrap Inc. (Tucson, AZ) to provide the engineering design and the FRP materials for this project.
DESIGN
The client, ADOT selected an externally bonded CFRP system for the strengthening and protection of several AASHTO Type II girders over 2 different bridges in Phoenix, AZ, 19th St and Jefferson St. QuakeWrap Inc. was selected as the CFRP engineering designer to restore the girders to their original performance capacities and develop construction documents for the installation of the repairs. ADOT, requested that moment capacity be restored to the girders and the amount of loss was up to 50% of the original capacity for the Jefferson St. bridge and 20% loss for the 19th St. bridge. Additionally, ADOT requested that 2 layers of fabric be installed similar to shear reinforcement to act as a protection system for securing the new flexural reinforcement and to act as a net holding spalled or impact damaged concrete from falling on vehicles below. QuakeWrap Inc completed all design work per the AASHTO Guide Specifications for Design of Bonded FRP Systems for Repair and Strengthening of Concrete Bridge Elements (1st Edition), as required by ADOT.
The first step in the design process required the evaluation of AASHTO Equation 1.4.4-1 which determines an element’s eligibility to be strengthened with CFRP.
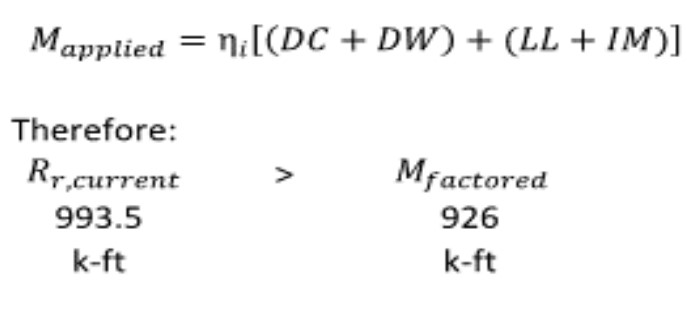
After it was determined that the girders were eligible for the repair with a CFRP system, engineers began to focus on increasing the flexural strength. Section 3.4 of the AASHTO code for flexural strengthening of reinforced concrete elements was followed for design purposes. The design approach is based on moment equilibrium and thus can be amplified to be used over a variety of girder shapes. The designs used different amounts of unidirectional CFRP layers installed at the bottom and lower bottom sides of the girders to meet the client’s need and such that the factored moment resistance was higher than the factored moment demand (Fig. 4). Many assumptions were made to carry out a design. The most significant assumption that was approved by ADOT was allowing the bridge deck slab to act compositely with the girder.
The key to meeting the design requirements on the Jefferson St. heavily damaged bridge girder was the addition of the longitudinal fabric on the sides of the girder. Fabric placed solely on the typical bottom surface would not suffice in this case. Every layer of CFRP fabric added takes a significant reduction in the allowable strain of that layer and continues to reduce for every layer after the first. This is due to the fact that all layers of fabric share the bond to the substrate with the first layer that is installed. Putting fabric on the sides reduces the contribution of the fabric by reducing the moment arm from the cross-section’s neutral axis. However, having more fabric with a first layer strain contribution far outweighed the slight reduction in the moment arm. Had it not been for the side installed fabric this girder would not have been retrofitted to the requested demand.
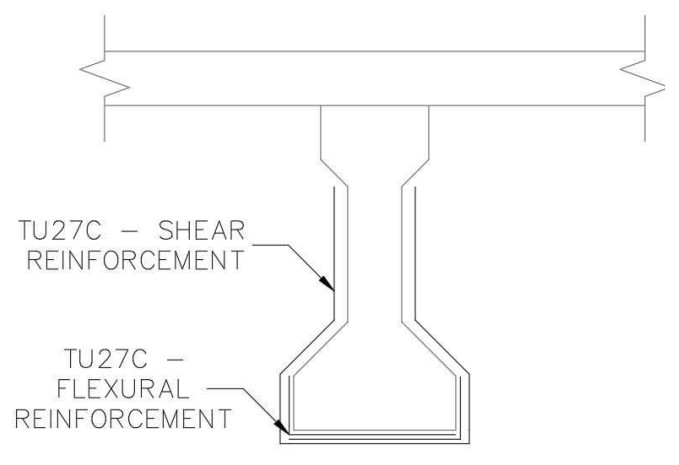
The flexural capacity of the girders that were retrofitted were calculated with unidirectional CFRP installed in the direction of the span of the elements, thus increasing their moment capacity by providing an FRP capacity to match or exceed the missing original capacity as shown. For Jefferson St. bridge, the additional strength provided by the CFRP system was:
M,;trp = 1,027 k-ft > Mreqa’ = 1,000 k-ft (ok)
For the girders in the 19th Avenue structure the additional strength provided by the CFRP was: M,;trp = 392 k-ft > Mreqa’ = 360 k-ft (ok)

Additionally, ADOT requested that a protection system be implemented to prevent concrete fragmentation due to spalling and/or impact of the girders. Bi-directional CFRP installed in a U-wrap scheme was initially decided and detailed as the best solution to use as a “net”, having strength in both directions. The 6-inch long carbon fiber tows in the bi-directional fabric are too short to properly develop strength and be effective. Furthermore, the short fibers make the installation of these strips and maintaining the alignment of the fibers very difficult. As the discussions with ADOT progressed, ADOT determined that it was in their best interested to use 6-inch wide unidirectional carbon strips (QuakeWrap® VU27C) with a 12 inch center to center spacing of the strips. After the first day of construction, ADOT agreed with the suggestion to switch the U-wrapped fabric to a uni-directional fabric and that is what was installed on both bridges.
Typical details of the CFRP installation drawings are provided in Fig. 5. All the CFRP fabric used was QuakeWrap® TU27C. The extent of the retrofit was limited to the regions indicated by ADOT; these regions were between 40′ – 50′ in length.
CONSTRUCTION PHASE/FIELD INSTALLATION
The construction phase of the CFRP repairs on ADOT project PHX-Cordes Jct. Hwy (1-17: 19th Ave. and Jefferson Street Bridges) was put out to bid and then awarded to FNF Construction out of Tempe, AZ. FNF Construction is a heavy civil general contractor with extensive experience working with ADOT, but lacking experience in the installation of CFRP systems. They subcontracted with FRP Construction LLC. to perform the strengthening system installation . This was to be the first CFRP repair done for ADOT and it required in depth work in all aspects of the project. From the planning through the execution phase, this project was unique in a variety of aspects.
During the planning phase, the project manager for FRP Construction was required to attend a weekly status meeting with FNF Construction and ADOT. These meetings included the review of material submittals, design modifications, and construction sequence scheduling. Before the project was allowed to be executed, every item was discussed in detail. All information had to be relayed to ADOT and accepted before any construction work could begin. These status meetings took place 1 month before the project was to be executed. Being that this was ADOT’s first CFRP repair, there were many questions to be asked and specifications to be modified. FRP Construction and its engineering partners QuakeWrap I nc. were able to successfully assist ADOT in providing adequate specifications that were feasible for a company to adhere to.
On April 24, 2017, FRP Construction began the CFRP install on the bridge girders. This work could only be done at night due to traffic restrictions. The available hours for work completion were from 9:00 P.M. to 5:00 A.M. The travel lanes of Interstate 17 were closed each night and reopened at exactly 5:00 A.M, to ensure traffic was not restricted during high vehicle volume use. A 6-man crew from FRP Constru ction performed this work within these time constraints. In addition to FRP Construction’s crew on site, FNF Construction provided a crew for traffic mitigation, concrete repairs and a final painting finish. Also, ADOT’s quality control team and design engineers made frequent visits to the sites for review and documentation purposes.
The location of the single damaged girder on Jefferson St. bridge and the installed flexural CFRP reinforcement is shown in Fig. 6.
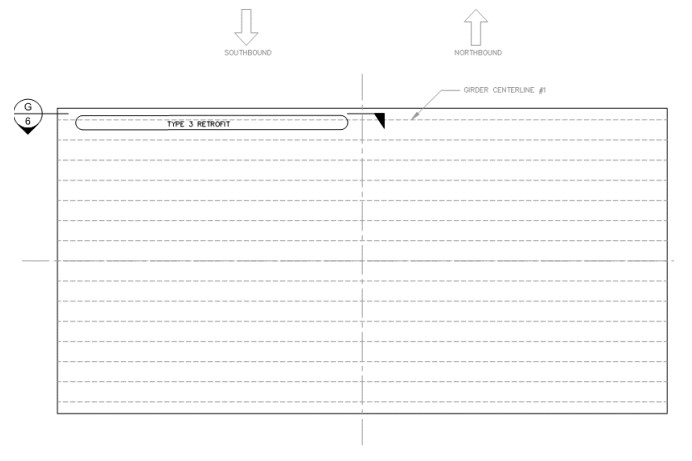
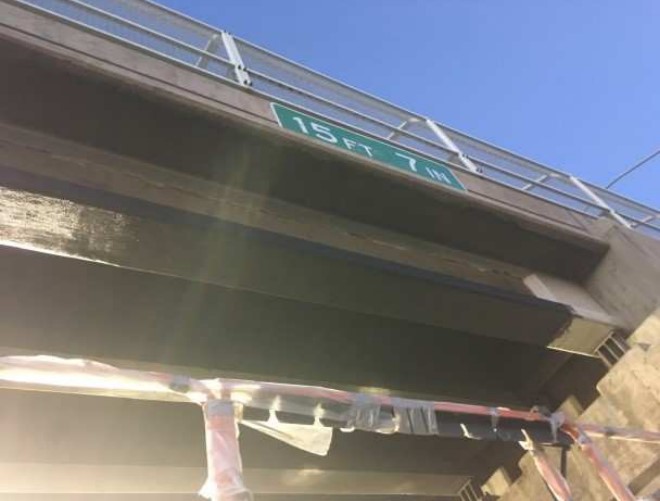
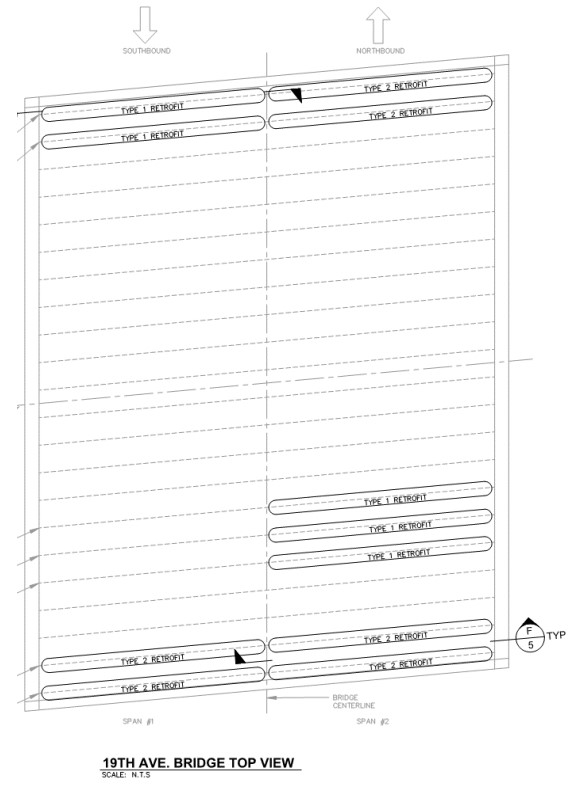
The full scope of the project also included repairs to an additional 11 girders on the 19th Ave. bridge (fig.7). The design documents provided by QuakeWrap Inc. detailed several types of repairs and which girders receive them. Some girders received both longitudinal fabric with U-wrap strips, while others just received the U-wrap strips.
The first day of CFRP construction efforts began at a slow pace. At the end of the first shift the expected progress was not met. FRP Construction knew one of the steps in the process was consuming a larger amount of man power than expected. The U-wrap strips were required on every girder in the retrofit plan and originally detailed by QuakeWrap using bi directional CFRP fabric. Cutting the TB20C biaxial fabric into small strips for the install proved to be a task that would likely exceed the time allotted to complete the project. FRP Construction requested that this fabric be cut off site in between shifts but was denied by ADOT due to quality control measures being used on site. In light of the time constraints, FRP Construction sent an RFI to QuakeWrap Inc. and obtained a design change that was approved by ADOT to install TU27C uni directional fabric as the 6-inch U-wrap strips. This fabric was much easier to cut and therefore quicker to install for the crew. With only one man-lift at our disposal, FRP was able to cut and install the fabric at a rate of about 500 SF per night.
FNF Construction scheduled the project to take approximately 20 working days for the fabric installs on the 19th Ave. bridge and requested that the Jefferson bridge be retrofitted over the span of one weekend starting Friday night at 9pm and ending Monday morning at Sam. FNF and ADOT were both very pleased to find the 19th Ave. bridge completed in approximately 15 days and the Jefferson St. bridge completed over the single weekend in May of 2017.
Quality controls for this project were specified by ADOT and added upon by FRP Construction. The materials provided by QuakeWrap Inc. were required to arrive on site in unopened packaging. The materials are identified and recorded by Lot numbers for the fabric and Batch numbers for the epoxy resin. FRP Construction, of their own accord, provided ADOT with a lay out of Lot and Batch numbers for each girder.
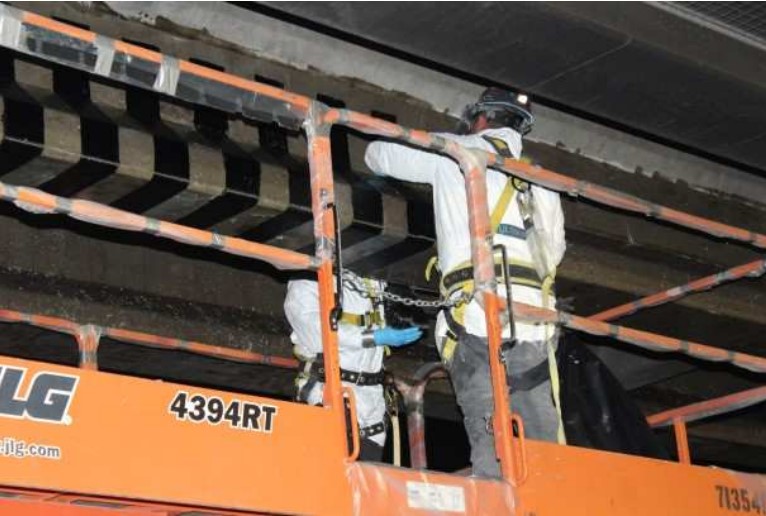

The project specifications required other quality controls using typical testing methods. FRP Construction subcontracted with Western Technologies of Phoenix, AZ to provide third party testing results to ADOT for the entire project. Multiple testing samples called witness panels, were made every day. One witness panel per day was required to be tested by Western Tech. The testing was performed using the ASTM standard D3039 and all the results were sent to QuakeWrap for verification. QuakeWrap assembled the results and submitted them to ADOT. Additionally, a couple of representative areas were prepared and tested for bond strength to the concrete substrate using ASTM C882 to guide the efforts. Those results were requested by ADOT’s QA representative even though they were not required per the published specifications and they were performed by FRP Construction.
FRP Construction planned and executed this project with the same commitment to quality that it brings to every project. Their attention to detail and safety have contributed to the unprecedented growth rate of this company over the years. The expertise and experience each employee brings to the table have helped FNF Construction deliver to ADOT another successfully completed project. Future endeavors of ADOT using CFRP have been strengthened, thanks to the efforts and experiences shared during this first project.
SUMMARY AND CONCLUSIONS
A total of 12 AASHTO Type II girders were repaired using CFRP products. One of the girders was severely damaged by a truck collision, resulting in a 50% loss of strength. The other 11 girders were not as badly damaged, resulting in a loss of 20% of flexural capacity. The repairs were successfully completed on schedule during evening hours and with minimal disruption to traffic . This positive first application of CFRP by ADOT will inevitably result in a wider use of this technology in Arizona and elsewhere.
ACKNOWLEDGEMENTS
The repairs discussed above were carried out by FRP Constru ction, LLC, Tucson, Arizona as a subcontractor to FNF Construction, Tempe, AZ.
REFERENCES
American Association of State Highway and Transportation Officials – Guide Specifications for Design of Bonded FRP Systems for Repair and Strengthening of Concrete Bridge Elements (1st Edition), AASHTO FRPS, 2012.
American Concrete Institute – Committee 440. Guide for the Design and Construction of Externally Bonded FRP Systems for Strengthening Concrete Structures, ACI 440.2R-08, ACI, Farmington Hills, MI, 2008.
Ehsani, M.R. and Saadatmanesh , H. “Fiber Composite Plates for Strengthening Bridge Beams,” Composite Structures, 1990, 15(4), 343-355.