The Global Leaders in Repair of Marine
Infrastructure
Used by the US Military worldwide, PileMedic® offers the most advanced systems for strengthening submerged piles, seawalls and bulkheads with minimal disruption of service.
What is PileMedic®
Developed by Prof. Mo Ehsani, PileMedic® is a patented unique engineered solution for repair and strengthening of columns and piles or piling on land and below water. Following three decades of research and development and several more recent investigations and testing by government agencies such as the U.S. Army Corps of Engineers, National Science Foundation, California DOT (Caltrans), Texas DOT, etc. PileMedic® has been adopted by many organizations including the US Military for its versatility, ease of installation, and unique structural strengthening features. It offers a rapid structural repair system for:
We invite you to download our sampled design details and specifications and become more familiar with our products.
You can visit this page for a quick review of the benefits of PileMedic and download a paper that summarizes the unique features and components of PileMedic.
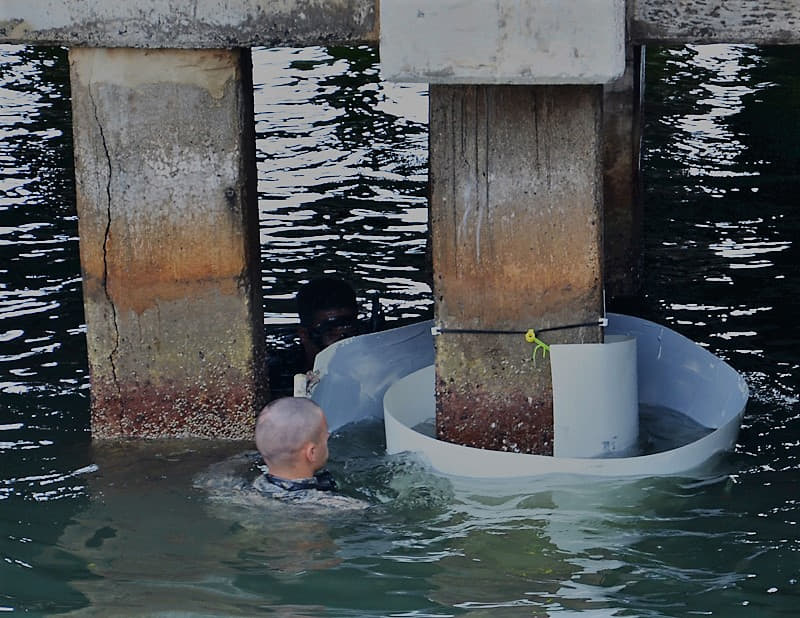
Difference Between Fabric and Laminate
Prof. Ehsani and his associates introduced the concept of strengthening of structures wet layup system (carbon FRP fabric) in the late 1980s and published these results in ACI in 1990. However, that technique has many shortcomings that limit its use in certain applications. That is why twenty years later, Prof. Mo Ehsani developed a new laminate system and introduced it in the same ACI publication. These laminates are constructed with specially-designed equipment. Sheets of carbon or glass fabric up to 9 feet wide (2.7m) are saturated with resin and passed through a press that applies uniform heat and pressure to produce the laminate shown here. The laminates offer several significant advantages compared to the fabrics used in wet layup applications, as listed below:
- Using a combination of unidirectional and/or biaxial fabrics, the laminates provide strength in both longitudinal and transverse directions; the tensile strength of these laminates can reach 155 ksi (1070 MPa).
- The laminates can be made as thin as 0.03 inches (0.76 mm); this allows them to be bent around a corner with a radius of 2 inches (50 mm).
- The laminates are manufactured in plants under high-quality control standards; this improves the quality of the finished construction.
- The strength of the laminates can be tested before installation; this assures the design engineer that the specified strength is met, eliminating delays for corrective actions.
- The repairs can be completed much faster in the field.
- The number and pattern of the layers of fabrics in the laminates can be adjusted to produce an endless array of customized products that can significantly save construction time and money.
- PileMedic® laminates are used to build a stay-in-place form around the column, creating an annular space that can be filled with concrete and reinforcing bars.
These PileMedic® laminates offer unique solutions that cannot be performed with the old wet layup fabric system. These include:
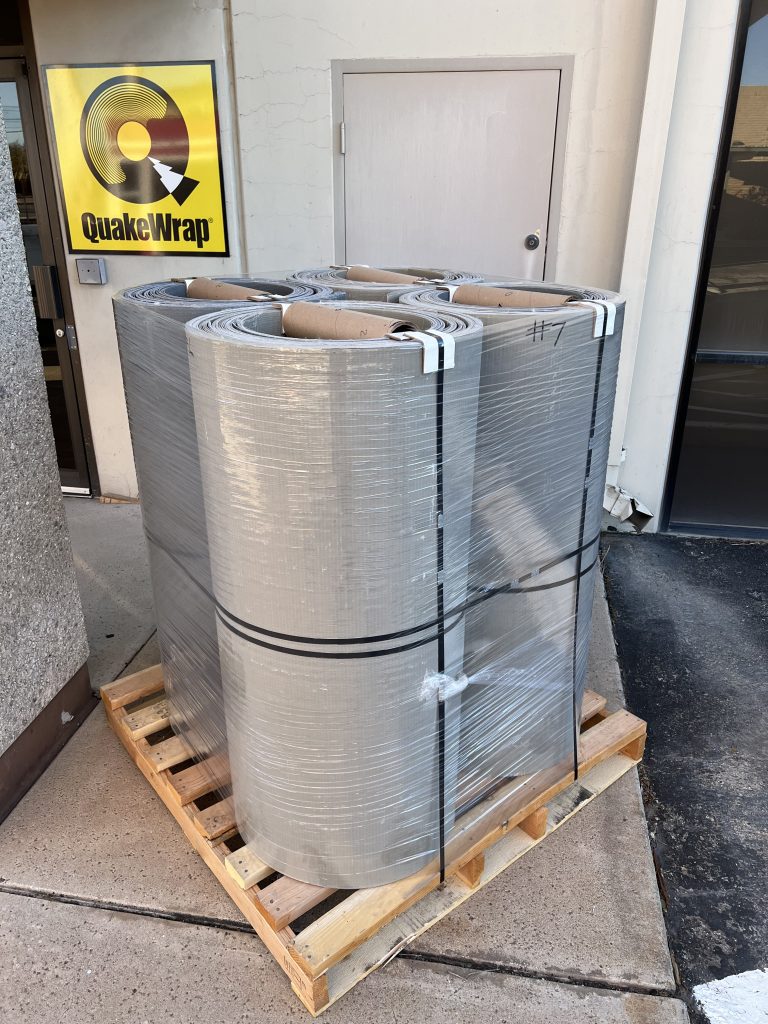
What is Sheet Pile Repair (SPiRe®)
Sheet Pile Repair (SPiRe®) is a very strong and rigid sandwich construction Fiber Reinforced Polymer (FRP) product that can be supplied in various geometrical shapes. The most common one is a 4-ft wide flat panel. In the field, these panels are secured to the corroded bulkhead or sheet pile with J-bolts. The edge of each panel is epoxy bonded to the adjacent panel to create an impervious stay-in-place form. The annular space between the SPiRe® panels and the corroded bulkhead is filled with concrete. Optionally, GFRP reinforcement can also be placed in the annular space.
Another application is for repair of beams and decks, where placement of concrete in such hard-to-reach areas becomes challenging. SPiRe® panels can be customized to fit the exact dimension of the beam or deck. Reinforcing elements can also be placed inside these elements. In the field, these shells are lifted and secured to the underside of the deck. The annular space between the shell and the deck or beam is filled with concrete. In both these applications, the SPiRe® solutions offers these advantages:
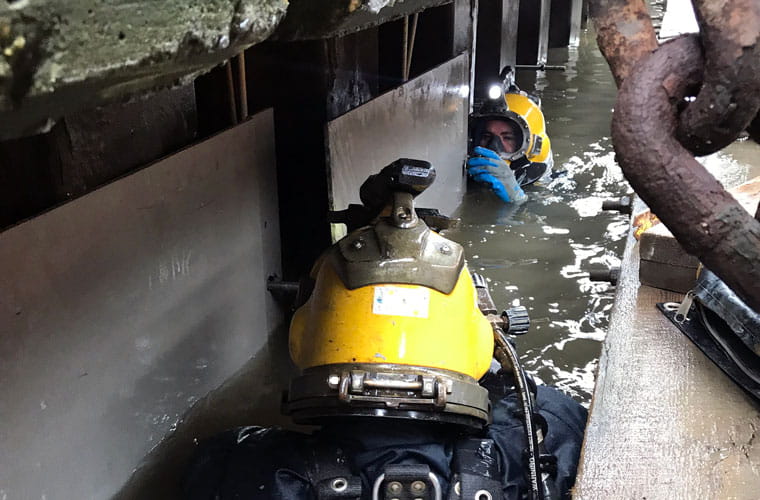
Components of PileMedic®
The PileMedic® system consists of a complete line of products for repair and strengthening of columns and piles that have been developed over a decade. These components include:
- PileMedic® laminates (4-ft long by various lengths)
- Spacers of various shapes and sizes to properly define the annular space and placement of longitudinal reinforcing bars (when required)
- Special epoxies that cure under water — eliminating the need for coffer dams
- Different solutions for sealing the bottom of the annular space
- Patented ShearWrap™ and ShearClamp™ for load transfer in repair of steel piles
- Underwater grouts and grout additives
How is PileMedic® installed?
Once the pile surface has been cleaned, the installation consists of the following steps:
- Pass the required number of spacers through zip-tie and wrap and secure the zip-tie and spacers on the pile; this step must be repeated every 2-3 feet along the repair height; watch video
- If required, snap the GFRP or steel reinforcing bars into the spacers
- Cut the required length of 4-ft wide PileMedic® laminate (watch video); standard detail requires wrapping the laminate twice around the pile (720 degrees) plus an 8-inch overlap. Make sure you use the circumference of the jacket including the annular space and not just the pile.
- Measure and mix the provided 2-part epoxy paste with the appropriate mix ratio until you achieve a uniform color mix. Alternatively, 900-ml packages are available that can be dispensed with a pneumatic gun and a static mixer.
- Apply the epoxy paste to the overlapping portion of the laminate (one circumference + 8 inches) with a thickness of 0.030 inches using a trowel
- Wrap the laminate around the spacers with the uncoated portion of the laminate in contact with the spacers; the second half of the laminate which is coated with epoxy will be wrapped around the first half.
- Tighten the laminate onto itself; at this stage the epoxy paste acts like a lubricant and allows for easy adjustments.
- Secure the laminate with a couple of ratchet straps to prevent it from unraveling while the epoxy paste cures.
- Repeat steps 4 through 8, overlapping each new jacket by 4 inches over the previously installed jacket; the overlap region must be coated with a layer of the same epoxy paste. Continue until a jacket of desired height (length) has been produced.
- Push the bottom of the jacket into the sea bed or use one of our bottom seal options to create a seal above the sea floor.
- Fill the annular space with the appropriate grout using the tremie method or pumps with the optional grout ports that we supply. It is recommended to fill the annular space for a height of 6-12 inches and allow that to set to form a seal before the jacket is filled to the top.
- Remove the ratchet straps.
Watch the PileMedic® User Manual Video made for the U.S. Army Corps of Engineers for their repair training below, or contact a PileMedic® technician today using the online form here.
Advantages of PileMedic®
Sample Project Videos
Over 500 timber piles restored while dock remained in service
Bulkhead repair at Port of West St. Mary includes SPiRe®, FRP rebar
Global Map of Sample Projects
Click the flag icon to see more details. Visit our Projects Page for project videos.