The cost of fixing a steel column is mainly influenced by the damage extent, material costs, labor rates, and any additional engineering or fabrication requirements that may arise due to the severity of structural issues. Average expenses encompass steel beam prices, professional contractor fees, and supplementary costs driven by labor, materials, and project-specific demands, all benchmarked against the prevailing market rate for professional contractors.
Repair methodologies, such as welding and reinforcement, require meticulous attention to detail, expertise in modern techniques, and adherence to building codes to guarantee structural stability and durability. Addressing structural issues promptly can also help reduce severe damage and cut down overall repair costs. Understanding these elements provides a foundational framework for estimating potential expenses, hinting at a broader spectrum of considerations that contribute to informed cost management.
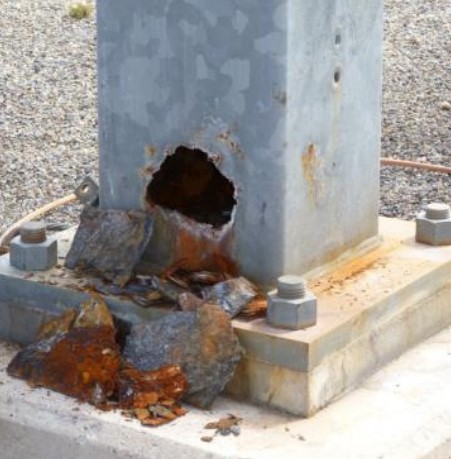
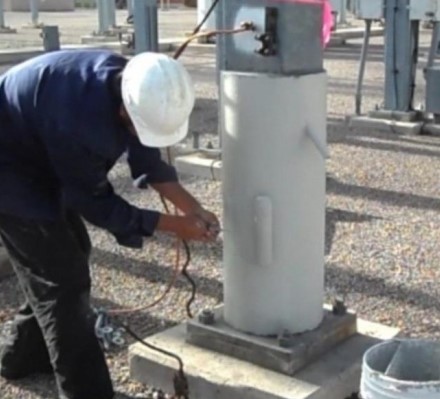
Key Takeaways
- Steel column repair costs vary based on the extent of damage and material costs.
- Labor rates significantly impact the overall cost of repairing steel columns.
- Additional engineering or fabrication requirements can increase the repair expenses.
- The use of modern welding techniques and materials like steel I-beams influences the cost.
- Prompt repair of structural issues can prevent more severe damage, reducing long-term costs.
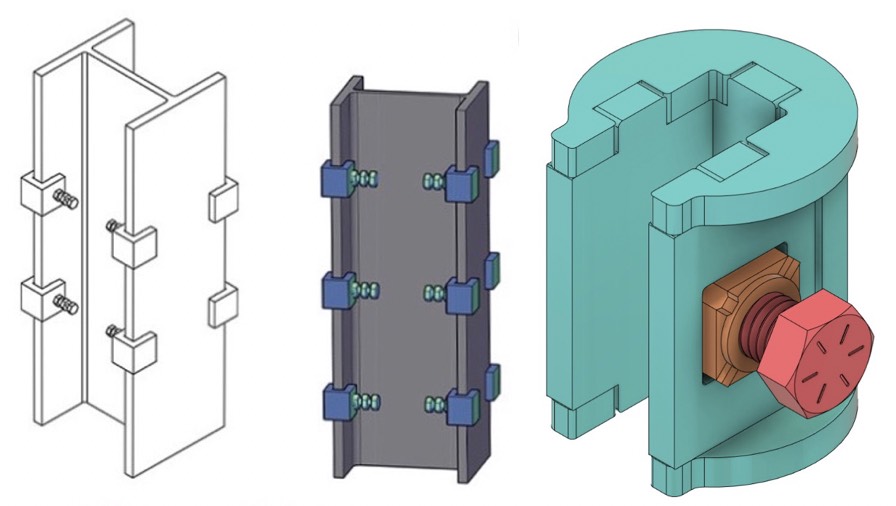
Estimate the cost of your Steel Column Repair Project
A steel column repair cost calculator is an invaluable tool for estimating the expenses involved in repairing or reinforcing a steel column. This calculator considers various cost factors, including the extent of the damage, the materials required for repair, and the use of specialized compounds like grout.
It delivers a precise estimate of the steel column repair cost, enabling property owners like you to effectively budget for the necessary repairs.
Steel Column Repair Cost Estimator
This pricing is for a jacket comparable to FRP form work WITHOUT needing vertical and horizontal hoop bars.
Want a detailed breakdown of your estimated cost?
Interested in specs and sample designs?
What Goes Into Steel Column Repair Costs
The cost of steel column repair is influenced by a variety of factors including the extent of damage, material costs, labor rates, and any additional engineering or fabrication requirements. When a steel column serves as a critical load-bearing wall and exhibits structural damage, the repair methods must be meticulously chosen. These methods can range from simple reinforcements to complete replacements, depending on the severity of the structural issues.
The cost of labor is a significant component, varying by location and the expertise of the foundation repair contractor hired. Additionally, fluctuating steel prices directly impact the overall cost. Proper assessment by professionals is essential to determine the best approach, ensuring the structure regains its integrity while managing expenses efficiently.
Average steel column repair cost
Understanding the average cost for steel column repair requires a detailed analysis of various factors, including labor, materials, and the specific requirements of the project. The financial implications hinge on the intricacies of each repair task, governed by the condition of steel columns, the chosen repair method, and the market rate for professional contractors.
- Steel Beam Prices: The cost of steel I-beams greatly affects the overall expense, fluctuating based on market demand and quality.
- Professional Contractor Fees: Expertise in structural repairs comes at a premium, with rates varying by region and the contractor’s experience.
- Additional Costs: Unforeseen complexities, such as access difficulties or the need for specialized equipment, can escalate the budget.
In essence, the average cost is not a static figure but a composite of several dynamic elements, each influencing the final financial outlay for restoring steel columns to their best condition.
Welding repairs
Welding repairs constitute a critical component in the restoration of steel columns, requiring meticulous attention to detail and expertise in modern welding techniques. These procedures are essential in addressing the integrity of steel beams, ensuring the load-bearing support beam continues to function at its best.
Whether it’s a beam replacement or a simple repair, the use of steel I-beams and steel posts is paramount. The process involves a thorough analysis to identify the extent of damage to the structural beam, followed by precise welding repairs. In cases where new sections are necessary, steel beam installation is carried out with precision to restore the structural integrity.
This technical approach not only guarantees the longevity of the structure but also enhances its capacity to withstand future stresses.
Reinforcement methods
Beyond welding repairs, reinforcement methods play a pivotal role in enhancing the structural resilience and longevity of steel columns. They employ a variety of techniques to safeguard the stability and durability of the construction.
- Installation of Steel Rods: This method involves embedding additional steel rods within or around the column, thereby reinforcing its structural integrity against stresses.
- Adjustable Steel Column: For areas requiring flexibility, adjustable steel columns can be introduced. They enable easy modification to accommodate building codes or support extensive repairs.
- Foundation Strengthening: Ensuring the concrete foundation is capable of bearing additional loads is essential. Techniques such as underpinning or the use of proper drainage systems prevent future deterioration, aligning with the type of repair method chosen.
These technical strategies are essential in maintaining the structural health of buildings. They adhere to stringent building codes while offering a pathway to freedom from structural vulnerabilities.
Importance of addressing structural issues promptly
Addressing structural issues in steel columns at the earliest opportunity is essential to preempting the escalation of damage and safeguarding the integrity of the construction. Early detection and correction of signs of damage can mitigate severe damage that compromises load-bearing beams and results in astronomical repair costs.
Structural issues, often stemming from improper installation or foundation shifts, require immediate attention to prevent a cascade of failures within the structural system. Precise, analytical assessment of steel columns for any signs of distress, followed by prompt intervention, is not just a cost-saving measure but a fundamental practice to guarantee the freedom of use and safety of the constructed environment.
As a result, a proactive stance on addressing structural concerns directly influences the longevity and resilience of steel column-supported structures.
Frequently Asked Questions
The historical value of a building can impact steel column repair costs due to preservation requirements and specialized restoration techniques often needed. Factors like architectural significance may influence repair methods and materials, affecting overall expenses.
Replacing a structural column can cost anywhere from $1,000 to $5,000, depending on factors like material, size, and labor involved. It’s essential to consult with a professional for an accurate estimate tailored to your specific needs.
To install a load-bearing column, costs can vary based on materials and labor, typically ranging from $1,000 to $4,000. Factors like size, location, and structural requirements influence the final cost.