Mooring Cells
Looking for Help with your Project?
Get free advice for any upcoming projects or repairs.
Mooring Cells
Mooring cells are frequently used in inland marine river ports and terminals to keep barge fleets aligned and to load and unload cargo. They are typically constructed of steel sheet pile panels that are driven into soil in a circular or rectangular formation and filled with soil or other granular materials as ballast to stabilize the structure. The fluctuations in water elevation along rivers leads to corrosion of the steel in the splash zone region which weakens the mooring cell structure. In extreme cases, shown here, large holes are formed in the mooring cell, allowing the ballast material to get washed out. This will further compromise the strength of the structure.
Current repair techniques typically involve patching or welding a steel plate over the damaged area. In some cases, a continuous steel band is welded around the area (like a belt). However, these steel elements will begin corroding soon, in the same way as the original structure.
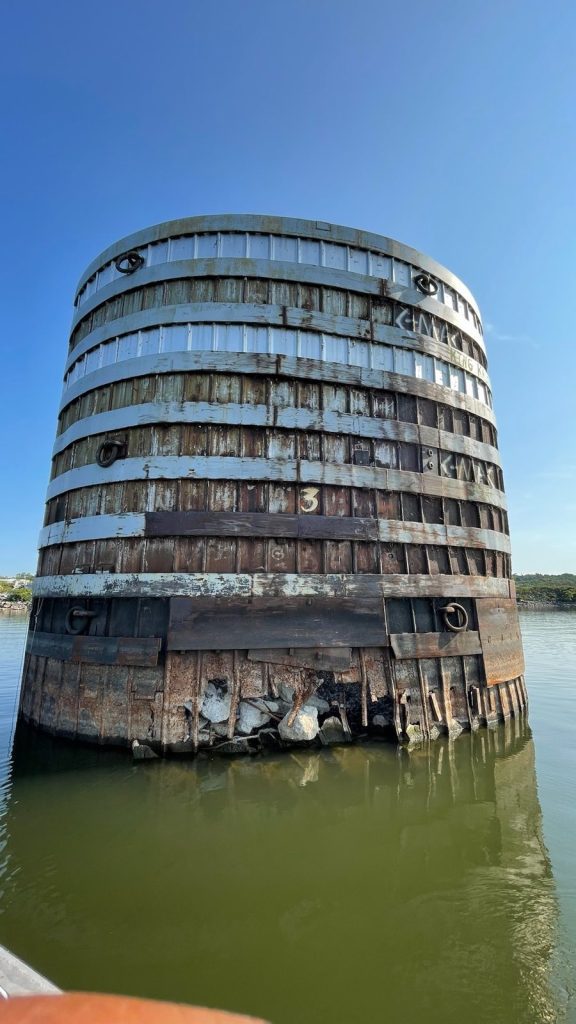
Solution
The patent-pending solution by Professor Ehsani presented here uses non-corroding high-strength FRP sheets, called PileMedic® . These laminates are available in 10-ft wide rolls, up to 500 feet long. If necessary, horizontal reinforcing bars can also be positioned around the cell. The PileMedic® laminate is wrapped once or more around the cell to create a small annular space; the overlapping end of PileMedic® can be coated with epoxy and optionally secured with screws.
The upper 4 inch edge of this shell is coated with epoxy and the finished shell is lowered into water. An additional 10-ft wide band of PileMedic® is similarly wrapped and bonded to the previous shell. This process is repeated until the desired height of the mooring cell is encapsulated.
The bottom of the shell is sealed and the annular space is filled with concrete or grout. Cut outs can be formed in the shell to allow access to the mooring rings and other hardware.
The strength of the shell provides confinement for the cell and the ballast; a single layer of PileMedic® is equivalent to #5 `(15mm) rebars at a spacing of 6 inches (150mm) along the height of the cell; wrapping the laminate twice, is equal to #5 (15mm) rebars at a spacing of 3 inches (75mm). If necessary, horizontal reinforcing bars can also be positioned around the cell prior to wrapping of the laminate.
The benefits of this system include:
- non-corroding FRP laminates with long service life
- Aesthetically pleasing finish
- Impervious shell that prevents moisture and oxygen reaching the steel cell and thus significantly reduces the corrosion rate.
- Smooth finish surface that allows for easier passage of debris around the cell.
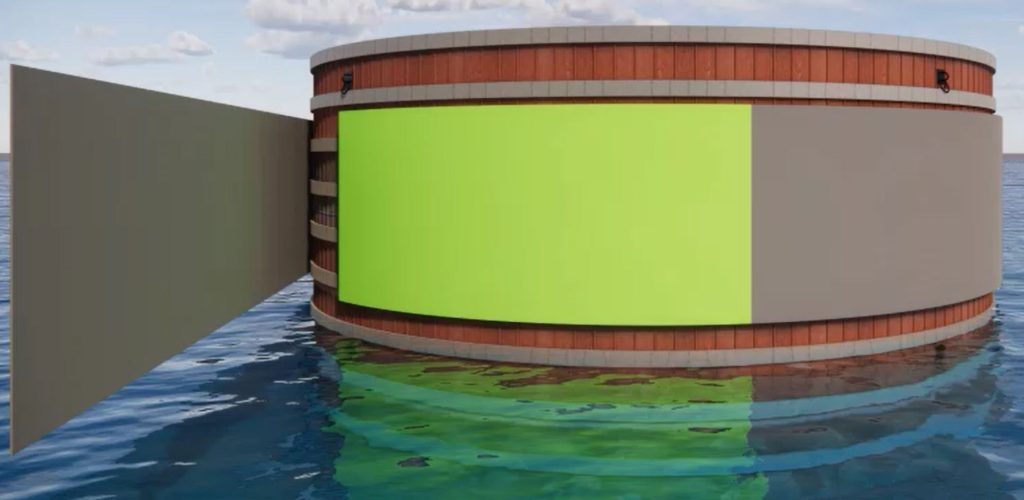
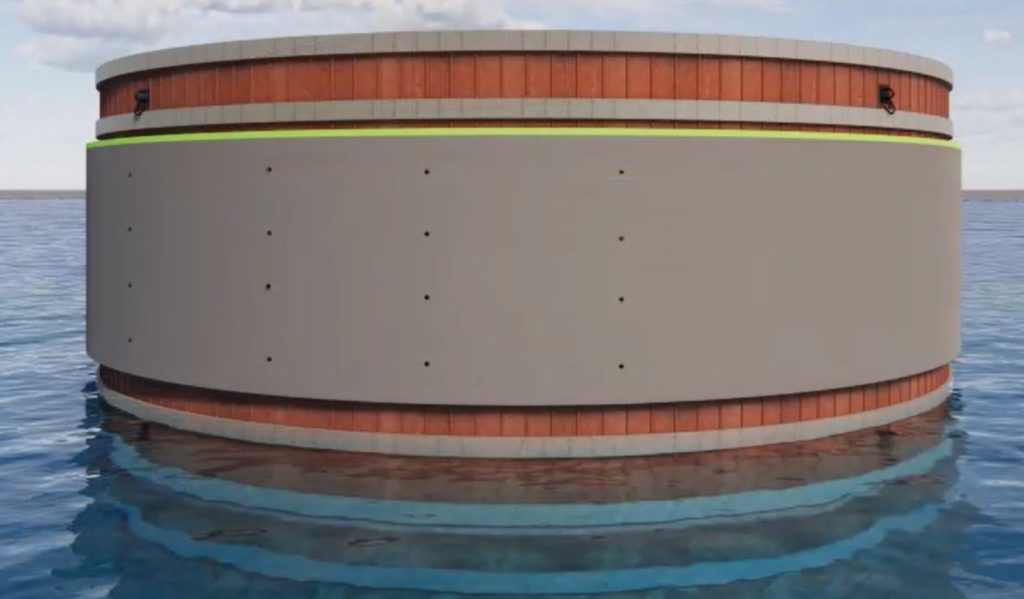
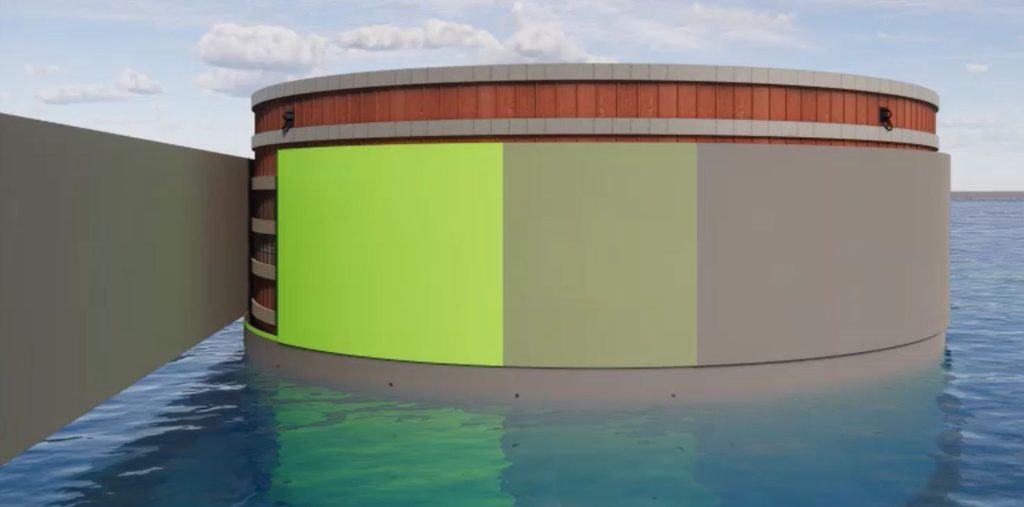
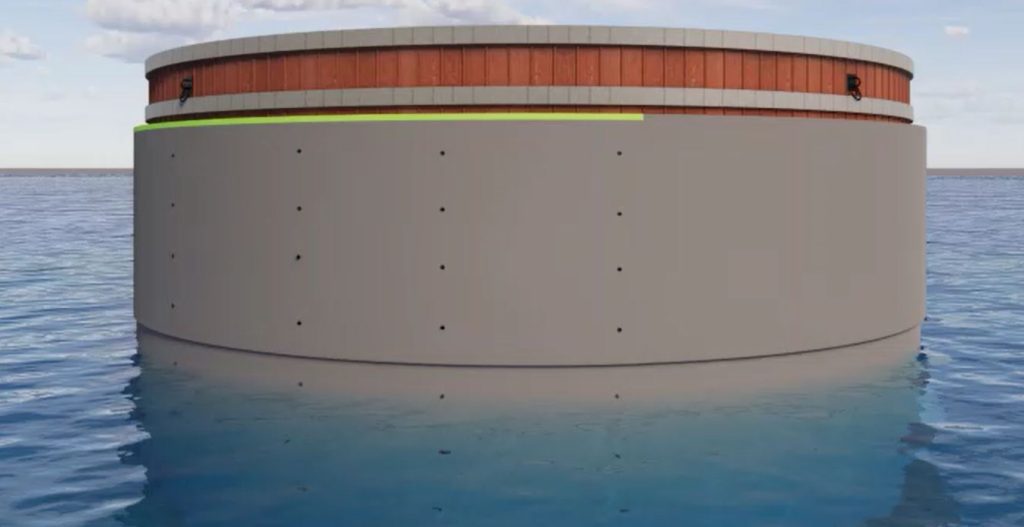
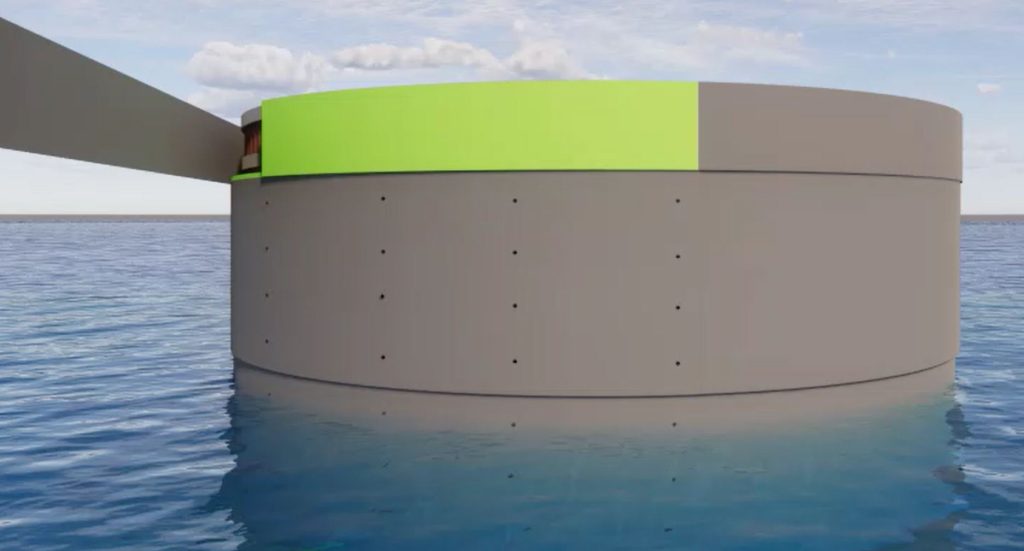
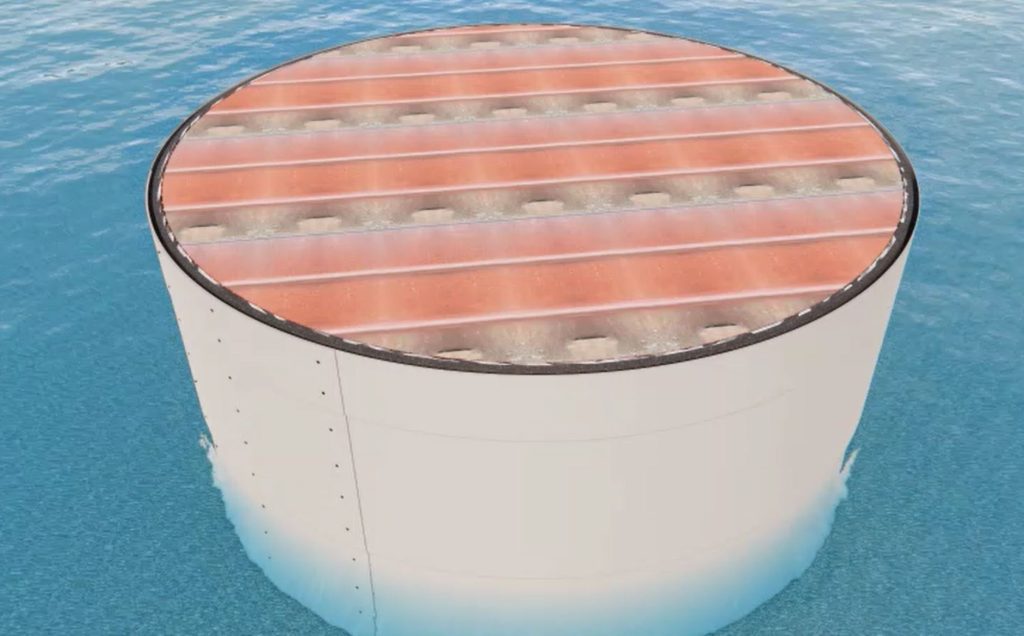
Video
This video shows an animation of the above process for repair of mooring cells.