Introduction
Sheet piles and bulkheads are frequently used in waterfront construction to retain and prevent erosion of soil. In most cases, the dry/wet cycle near the splash zone, defined as the region between the low and high tide water levels, gets damaged with age. If the seawall is made of reinforced concrete, water penetrates through the cracks in concrete, causing corrosion of the reinforcing steel. Similarly, walls made with steel or timber get damaged and weaken with age. In extreme cases, the section losses are large enough to allow soil to wash out through cracks and holes in the wall (Fig. 1), that could cause settlement in the ground supported by the bulkhead. In most cases, the portion of the seawall that is embedded in soil remains relatively undamaged because the lack of oxygen at those depths cannot support the ongoing corrosion of the wall.
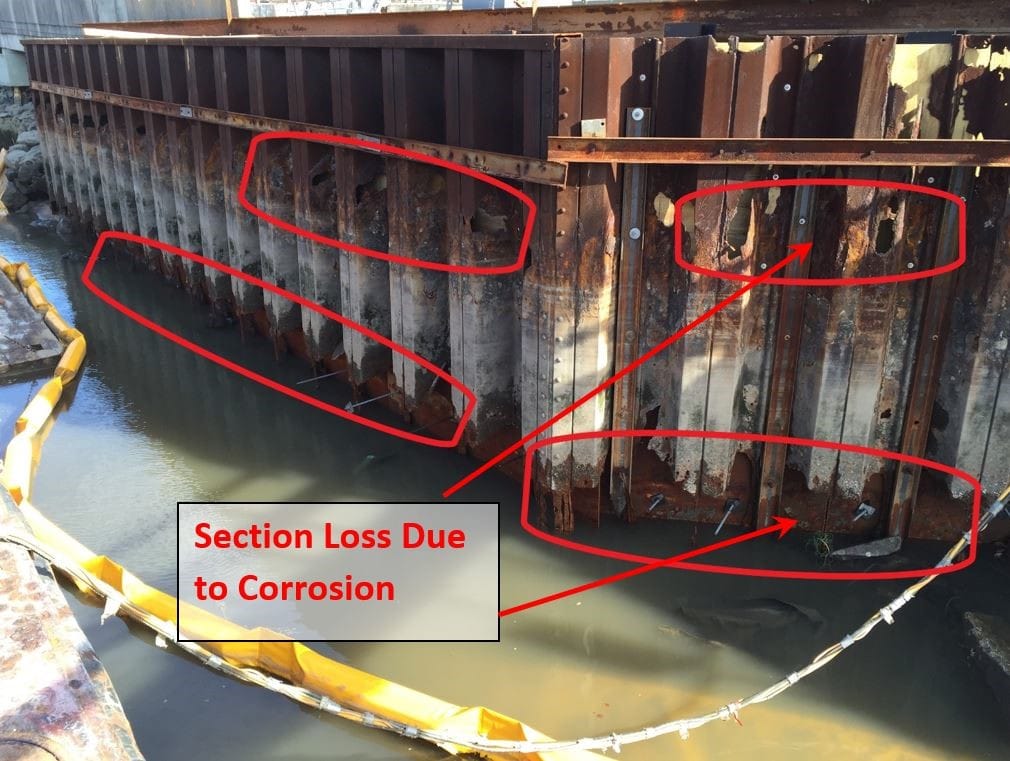
Following decades of research and development, the author has recently received a patent on a system for repair of such structures that is presented here (US Patent #10,968,631).
Current Repair Techniques
There is not a universally accepted method for repair of corroded seawalls. In some cases, when there is significant loss of the steel thickness or section loss, new steel plates can be welded to the corroded wall. However, obtaining permits for welding under water is difficult and the cost of such welding is significant. Furthermore, just as the original seawall corroded, the unprotected repaired steel wall is susceptible to corrosion.
Another repair technique is to clean the surface of the wall from any rust and then apply a layer of a corrosion-inhibiting paint. The logic is that the applied coating will deprive the steel wall from exposure to oxygen and water and this will stop the corrosion process. While this solution may seem reasonable, there are two problems with this approach. First, this method requires the construction of a coffer dam in front of the wall and dewatering the area to give the crew access to the wall; this is a costly process, especially in deep waters. Second, the longevity of any coating applied will remain a concern. Once that coating begins to crack, water and oxygen will penetrate through those cracks, fueling the corrosion process.
Sheet Pile Repair (SPiRe®) System
The recently developed and patented system described here overcomes the above shortcomings. The solution is called Sheet Pile Repair (SPiRe®) system. SPiRe® is comprised of rigid Fiber Reinforced Polymer (FRP) panels that are custom made for each project. The panels follow the sandwich construction technique that is commonly used in aerospace and shipbuilding industries. A proprietary lightweight core around 0.2-0.3 in. thick is sandwiched between one or more layers of unidirectional or biaxial glass or carbon fabric. The core thickness and the type and strength of the fabric layers is a function of the project requirements and will be designed for each application. The overall thickness of the product is typically less than 0.5 in. (Fig. 2).
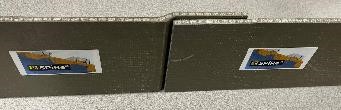
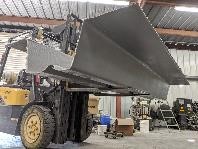
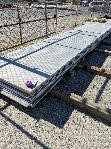
The panels are made using a resin infusion process. As shown in Fig. 2, these could be custom made to any shape to match the existing wall geometry. However, the most common are the flat panels that are 4 ft wide. They can be manufactured in any length and can also be cut to the desired length in the field. While the panels can be used for structural strengthening, the projects completed to date have been for providing a corrosion protective system for the walls only.
Field Installation
In the first application of the SPiRe® system, a 926-ft long wall varying in height from 4-14 ft was repaired in Chesapeake, VA. The corrugated metal sheet pile is part of a pulp and paper factory and was severely damaged by corrosion. The owners were concerned about chemicals on the plant ground leaching through the wall into the river causing damage to the environment.
The construction steps are shown in Fig. 3. Holes are cut in the steel sheet pile and stainless-steel J-bolts are used as tie-down elements. The J-bolts are secured to the wall using a washer and a nut. When required, reinforcing bars can also be placed in the cavity of the wall. It is preferred to use glass FRP bars for such applications to eliminate any concern for future corrosion of these bars. The panels have a 4-in. wide depressed lip along one of the long edges (Fig. 2) that is used for connecting the panels together. A special underwater epoxy paste is applied to create a sealed overlapping region. The panels are also secured to the seawall along those overlapping edges with the J-bolts at predetermined locations. This creates an impervious stay-in-place form in front of the deteriorated seawall. If necessary, whalers can also be temporarily placed horizontally to prevent excessive deflection of the panels during the placement of the grout.
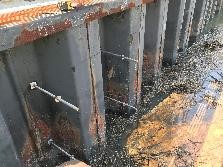
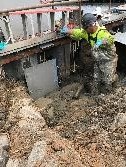
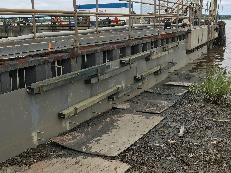
The bottom of the panels can penetrate by about 16-20 in. into the soft silt at the riverbed. In other applications, a temporary seal can be produced at the lower elevation where the panels end. When placing the grout by the tremie method, about 6 to 12 inches of grout is placed along the base of the wall and allowed enough time for this grout to harden and create a seal. The remaining height of the wall can be filled with grout in a single lift if desired. The whalers are removed, and the ends of the J-bolts can be trimmed and if desired, covered with a cap.
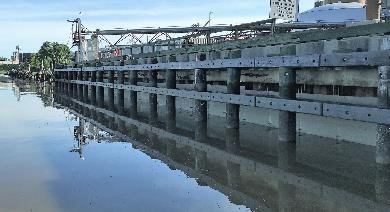
The repair system which is a combination of the FRP SPiRe® panels and the grout provides an impervious layer. This system will prevent moisture and oxygen reaching the corroding wall. Because oxygen is the fuel to the corrosion process, by depriving the wall of this fuel source, the corrosion process comes to near halt. For this project, the impervious wall will also prevent leaching of any toxic materials from the plant into the river. A video of this project is available at: www.TinyURL.com/SPiRe-WestRock
Among the advantage of this solution is that it eliminates the need for coffer dams. Also, the lightweight panels can be easily lifted by workers, making the installation much easier and faster for hard-to-reach areas. The repair system includes no steel components that could corrode. Once installed, the solution is expected to provide a 50+ year service life of virtually maintenance free protection for the wall.
Several ports and private piers have been repaired with this technique to date. A major upcoming project is in the port of Melbourne, Australia where a 1 km long seawall is scheduled for repair in 2023. The US military has also used this solution on several projects globally including at this Coast Guard facility in Tongue Point, Oregon: www.TinyURL.com/SPiRe-USCG. This video shows another application for repair of corrosion-damaged steel bulkheads at the Port of West St. Mary, LA: www.TinyURL.com/SPiRe-StMary
While the applications to date have been to repair and prevent further corrosion of the walls, the SPiRe® system can be designed to contribute to the load-carrying capacity of a wall also. Such repair options must be evaluated and designed for on a case-by-case basis.
The General Contractor for the project described in this paper was FRP Construction LLC, Tucson, AZ. The diving subcontractor was Crofton Industries, Portsmouth VA. The efforts of both these companies is gratefully acknowledged.