Seawalls and bulkheads play a vital role in safeguarding coastlines and properties against the relentless power of the ocean. However, these protective structures are not immune to wear and can deteriorate over time, especially if not inspected regularly.
This article delves into the common failures of seawalls and explores the precise and technical methods used for their repair. By understanding these failures and implementing timely repairs, property owners can ensure the longevity and effectiveness of their seawalls and bulkheads in defending against coastal erosion and water damage.
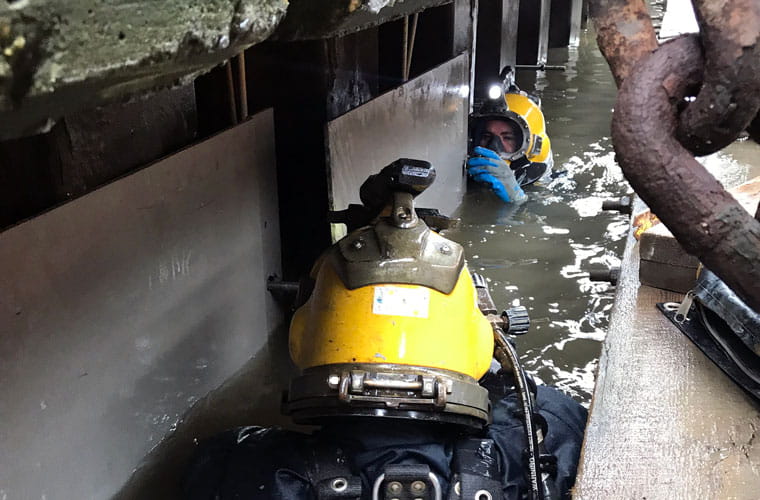
Why Do Seawalls Fail
Seawalls can fail due to a variety of factors, most notably poor maintenance and the effects of natural elements.
- Prolonged exposure to saltwater and harsh weather can cause the seawall to deteriorate, further compromising its integrity.
- Poor maintenance can lead to the deterioration of the seawall or bulkhead over time, making it more susceptible to structural damage and water damage.
- Hydrostatic pressure can cause the seawall to bow, lean, or develop cracks, allowing water to penetrate and erode the soil behind the wall.
- In seawalls and bulkheads made of timber, the dry/wet cycles can cause the wood to rot and lead to failure of the seawall.
It is important to address these issues promptly through seawall repair to prevent costly repairs and ensure the longevity of the seawall. If not attended to, the soil behind the seawall can wash out and leading to the collapse of the seawall. This loss of soil often can be detected by a dip in the land area adjacent to the seawall (e.g. the parking lot or yard).
Common Types of Seawall Failures
Common types of seawall failures can be attributed to a lack of maintenance, corrosion caused by saltwater exposure, joint separation, and hydrostatic pressure.
Failure to properly maintain seawalls can lead to cracks, deterioration, and structural issues.
Corrosion from saltwater can weaken the materials of the seawall (in steel sheet piles or reinforced concrete seawalls), while joint separation and hydrostatic pressure can cause panels to shift or break, compromising the integrity of the seawall.
Understanding these common failures is crucial in implementing effective repair strategies.
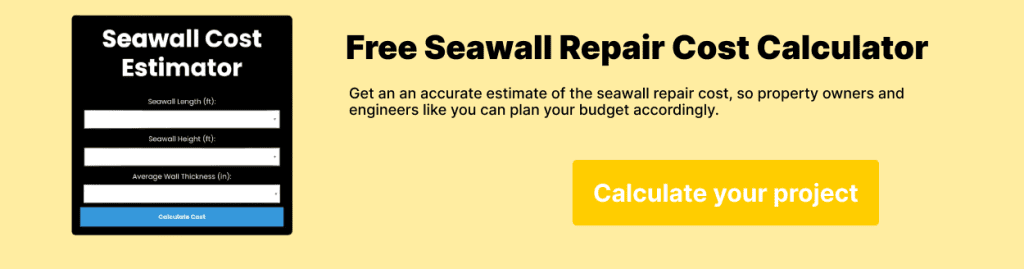
Lack of Maintenance
It is crucial to prioritize the upkeep of concrete seawalls to ensure their structural integrity and longevity. Here are three common consequences of a lack of maintenance:
1. Seawall Damage: Without regular inspections and maintenance, small cracks and defects in the seawall structure can go unnoticed and worsen over time. This can lead to water infiltration, erosion, and the weakening of the seawall’s overall stability. At a minimum, the salt water could penetrate these micro cracks and cause corrosion of the reinforcing steel in the wall. Because the corroded steel takes a larger volume, this expansion causes further cracking and breaking of the concrete that is covering the steel rebars.
2. Increased Repair Costs: When maintenance is neglected, minor issues can escalate into major problems that require extensive repairs. Timely identification and resolution of seawall concerns can help prevent costly repairs in the long run.
3. Compromised Seawall Solution: A neglected seawall is less effective in protecting properties from the force of the ocean and natural elements. Regular maintenance ensures that the seawall remains a reliable defense against water and erosion.
Failure to address these maintenance issues can result in further damage, including corrosion due to salt from the water. In extreme case, the buildings supported above the seawall or bulkhead could slide into the sea or river with potential for loss of lives.

Corrosion due to salt from the water
Seawater is corrosive and easily damages steel sheet piles. The damage is most severe over the splash zone region defined between the low and high tide water levels. If unattended, corrosion can lead to thinning and ultimately tearing o the sheet pile. The missing sections cause loss of strength in the sheet pile which could be a safety concern. The holes formed in the wall allow loss of backfill and soil. This can be detected by settlement of land behind the wall; sometimes this is seen in sagging areas that collect a puddle of water. These signs indicate loss of soil and must b investigated.
Saltwater is naturally corrosive and can infiltrate the concrete of seawalls, leading to the corrosion of the steel rebar inside. This gradual process of corrosion weakens the structure of the seawall and can eventually lead to failure if not addressed. The expansion of the corroded rebar puts pressure on the rest of the structure, exacerbating the damage. To emphasize the impact of corrosion due to saltwater, consider the following table:
Type of Seawall | Type of Damage |
Wood or Timber | Wood rot due to moisture |
Steel Sheet pile | Corrosion and weakening of steel; large gaps in steel could lead to loss of backfill soil |
Concrete | Cracking of concrete and corrosion of rebars |
These failures occur as a result of the corrosion process and can compromise the integrity of the seawall. Effective methods for repairing corrosion damage include sealing cracks, reinforcing the structure, and implementing erosion control measures. Regular inspections and maintenance are essential to prevent and address corrosion issues on time.
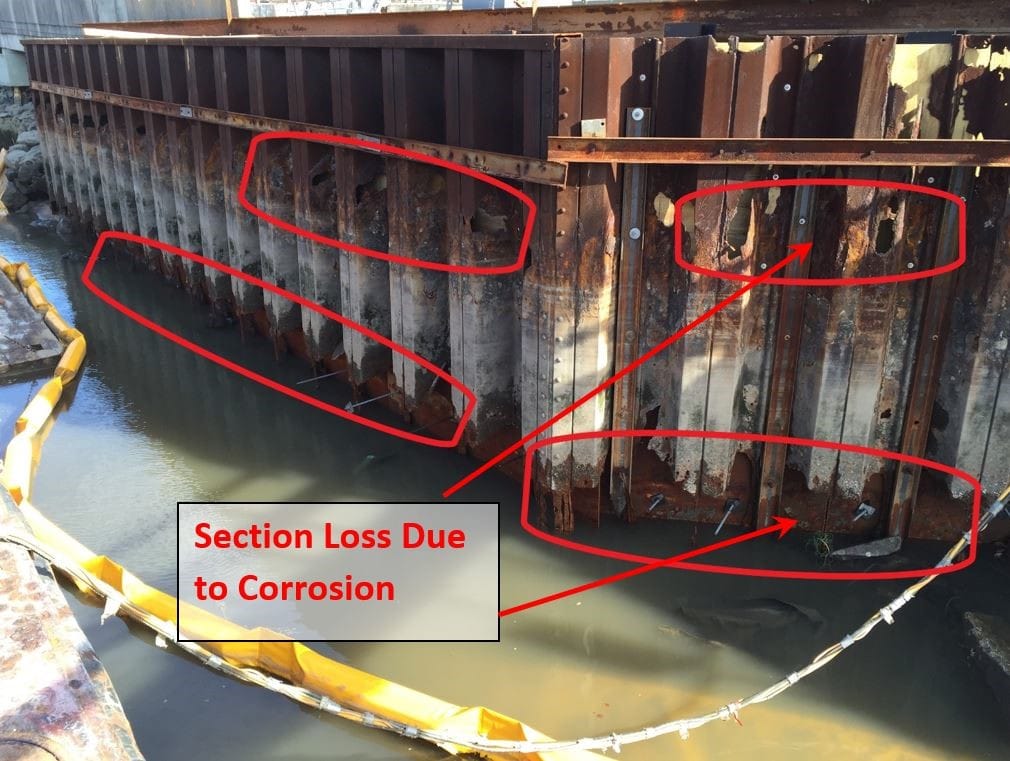
Joint Separation
Joint separation is a significant concern in seawall failures. It occurs when panels move vertically apart, allowing soil to pass through the openings and compromising the structural integrity of the seawall. This common type of failure can be attributed to various factors such as structural faults, age, settling, and inadequate anchoring. In timber seawalls, the horizontal joint between the panels could deteriorate and move, leading to loss of soil and weakening of the seawall.
Here are three important points to consider when addressing joint separation in seawall repair:
1) Identification: Thorough inspections should be conducted to identify any signs of joint separation. These signs may include visible gaps between panels or soil erosion around the seawall.
2) Repair Methods: Once joint separation is identified, appropriate repair methods must be employed to restore the structural integrity of the seawall. This may involve reinforcing the joints, filling the gaps with suitable materials, and ensuring proper anchoring to prevent future separation.
3) Importance of Timely Repair: Quickly addressing joint separation is crucial to prevent further damage and erosion. Ignoring this issue can lead to more significant failures, such as cap breakdown or waterline cracks caused by hydrostatic pressure.
By addressing joint separation in the repair process, the seawall can be effectively restored and protected against the damaging effects of erosion and other common failures.
Transitioning into the next section, we will now discuss the impact of hydrostatic pressure on seawall integrity.
Hydrostatic Pressure
Continuing the discussion from the previous subtopic on joint separation, the impact of hydrostatic pressure on seawall integrity must be examined.
Hydrostatic pressure refers to the pressure exerted by water when it is at rest. In the case of seawalls, hydrostatic pressure can cause significant damage and lead to common types of failures.
One such failure is waterline failure, characterized by horizontal cracks caused by aging concrete, rod corrosion, or the pressure exerted by the water.
Another type of failure is toe and berm failure, which occurs when the berm at the bottom of the panels is lost due to fast currents and wave movements. This can result in cracked or tilted panels, rotated or broken caps, and gaps between the seawall and support pilings.
Hydrostatic pressure can also contribute to cap breakdown, where the cap cracks or breaks away due to corrosion or panel movement, leading to sagging or crooked panels.
Property owners need to address hydrostatic pressure issues promptly to prevent further damage and ensure the longevity of the seawall. This can be achieved through effective seawall repair techniques that address the underlying causes of failure and promote customer satisfaction.
Seawall Repair Case Studies
Seawall Repair Methods
Seawall repair methods encompass a range of techniques, including:
– The use of FRP panels (SPiRe+)
– Polyurethane crack injection
– Structural epoxy injection
– Soil stabilization injection grouting
These methods are designed to address specific issues such as cracks, voids, and soil instability, ensuring the structural integrity and longevity of the seawall.
FRP panels (SPiRe+)
FRP panels have emerged as a time-efficient and cost-effective solution for seawall repair. These panels consist of lightweight honeycomb or 3D fabric sandwiched between resin-saturated FRP fabric sheets.
Here are three key advantages of using FRP panels for seawall repair:
1. Fast and economical repair: The lightweight nature of SPiRe+ panels allows for quick installation, reducing repair time and costs.
2. Corrosion resistance: Unlike traditional materials like steel or timber, FRP panels do not corrode. This eliminates the need for frequent maintenance and extends the lifespan of the seawall.
3. Moisture and oxygen barrier: The impervious nature of SPiRe panels prevents the influx of moisture and oxygen, which are key factors in the corrosion process. This significantly lowers the corrosion rate and enhances the durability of the seawall.
Polyurethane Injection
Polyurethane injection is not really a method for repairing or restoring the structural strength of the seawall. Instead, it stabilizes the soil behind the wall. This method involves injecting polyurethane resin into the cracks and the cavity behind the wall to seal and stabilize the structure. There are a number of foams and urethane grouts made by several manufacturers that can be used for this application. Polyurethane or foam can be injected behind the seawall (on the land side). These products react with the moisture in the soil or any water that is leaking through the cracks in the seawall. This reaction causes expansion of the urethane and it seals the cracks and creates an impervious barrier on the land side behind the seawall. The foams also fill any cavities in the soil that may have resulted from loss of soil through cracks. It is also used for concrete leveling, where the resin is injected underneath the sinking concrete to lift and level it. High-quality materials, such as polyurethane grouts, are essential for achieving long-lasting results.
By utilizing polyurethane crack injection, seawall owners can ensure the integrity of their structures and prevent further loss of soil. However, this technique does not address any loss of strength in the wall that may have occurred due to corrosion of steel, cracks in concrete or rot in timber piles.
Transitioning into the subsequent section about structural epoxy injection, this method is another important technique for seawall repair.
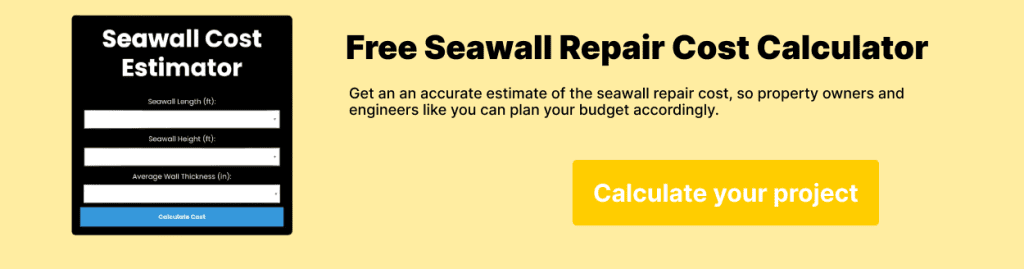
Structural Epoxy Injection
Structural epoxy injection is a widely utilized method for repairing and reinforcing all concrete structures including seawalls. It has no application in steel sheet piles and may be beneficial for repair of timber seawalls in some special cases. This method involves filling and sealing cracks and voids in the concrete, while also providing structural adhesive strength. However, bear in mind that the strength of a concrete structure comes primarily from the tensile strength of reinforcing steel and the compressive strength of the concrete. Therefore, any amount of epoxy injection will NOT add to the strength of the seawall or bulkhead.
Here are three key aspects of structural epoxy injection for seawall repair:
Diagnosis of seawall problems: Before initiating a seawall repair project, a thorough diagnosis of the seawall is necessary to identify the specific areas of damage and determine the cause of the formation of cracks. While prestressed concrete is designed to remain crack-free during service, the more conventional “reinforced concrete” structures are expected to have minor hairline cracks at service loads. The problem with seawalls is that these fine cracks allow the ingress of saltwater and that leads to the corrosion of reinforcing steel. Since rust increases the volume of the steel, it forces the concrete to crack further or even ave parts of the concrete to spall off.
The only benefit of epoxy injection is that it will seal the crack and prevent penetration of water. This prevents or slows down the corrosion of reinforcing steel in concrete seawalls. As such, epoxy injection prevents further deterioration and corrosion of the concrete wall. If there is any loss of strength in the seawall due to corrosion of reinforcing bars, the injection of cracks with epoxy will NOT restore that lost capacity to safely withstand the forces of soil, waves and tides.
If it is decided to inject the cracks with epoxy, there are many concrete contractors that can perform this task. It is a good idea to seek a contractor that has been trained by the American Concrete Institute (ACI) in this field. The procedure requires sealing the crack with a quick setting epoxy (to make sure the injected materials stay in place). Injection ports are inserted along the crack. A low viscosity epoxy is injected from these ports into the cracks. Qualified contractors know what procedure to follow so that there are no voids left behind and the crack is completely filled with epoxy.
Soil Stabilization Injection Grouting
Soil stabilization injection grouting is a crucial method for repairing and reinforcing seawalls, providing essential stability and strength to the surrounding soil and substrates. This technique involves injecting grout into the soil to reduce its permeability, preventing soil loss, erosion, and water infiltration. The grout forms a solid, impermeable mass that supports footings and foundations, ensuring the structural integrity of the seawall. Two common types of injection grouting for soil stabilization in seawall repair are permeation grouting and curtain grouting. Permeation grouting involves injecting grout into compacted soil to improve its strength and reduce permeability. Curtain grouting involves injecting grout through injection soil lances to create a continuous barrier that stabilizes the surrounding soil. This method is particularly effective when the seawall is in contact with soil moisture, preventing erosion and maintaining the stability of the seawall.
Certainly, here is the information you provided formatted into a table:
Injection Grouting Methods | Description |
---|---|
Permeation Grouting | Injecting grout into compacted soil to improve strength and reduce permeability |
Curtain Grouting | Injecting grout through injection soil lances to create a continuous barrier for soil stabilization |
Step by Step Seawall and Bulkhead Repair
The 3-ft (900mm) wide panels are available in any length. The panels are connected to the corroded seawall with anchor bolts on an approximately 3 ft x 3 ft (1m x 1m) grid to create a very large structural wall in front of the deteriorated bulkhead.
The annular space between the wall and these panels is filled with concrete or grout. A unique feature of this patented system is the T profiles on the back face of the panels. That surface is also grit coated for improved bonding to concrete. The T profiles act as reinforcing bars that are permanently attached to the panels. The panels are amazingly strong.
The SPiRe+ panels have a tensile strength equal to No. 5 Grade 60 steel reinforcing bars at a spacing of 2.5 in. (or 15mm, 400MPa bars at a spacing of 65mm). The panels have no corroding elements, thus lasting forever and ensuring a durable and sustainable repair.
Resources
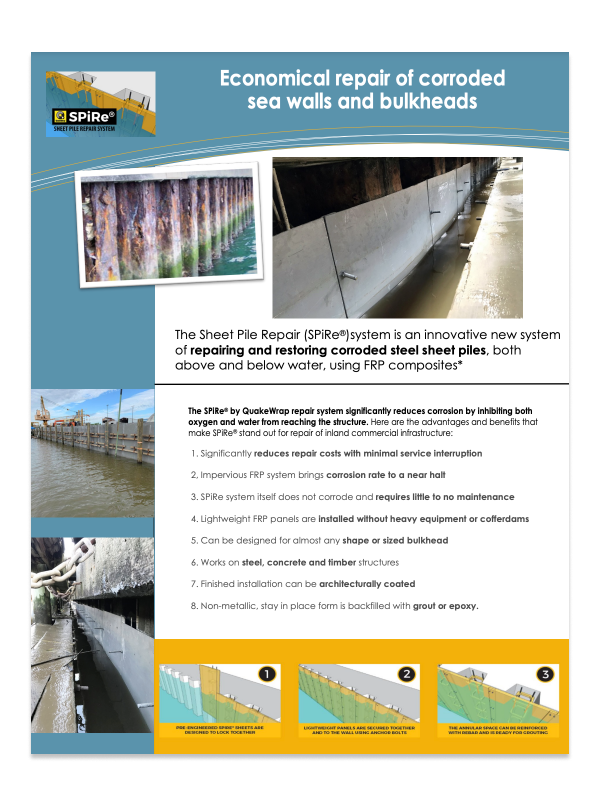
SPiRe Product Brochure
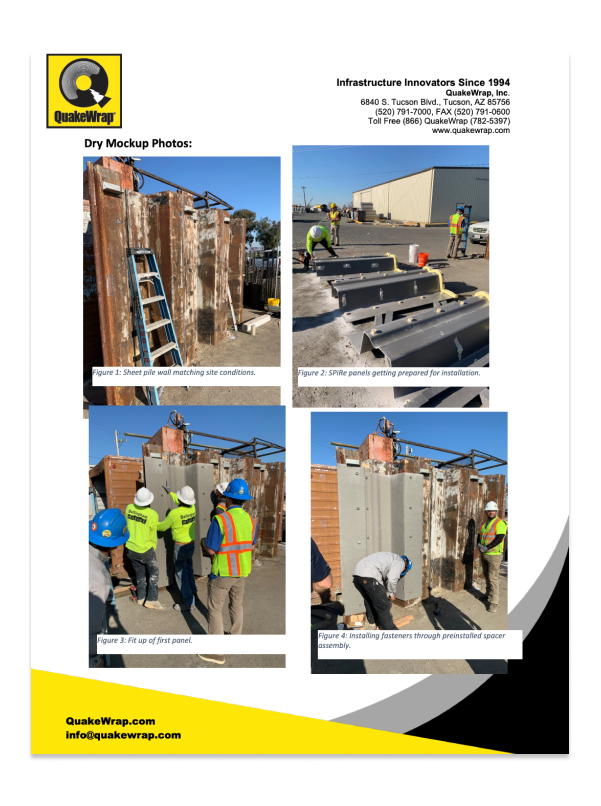
SPiRe Project Profile
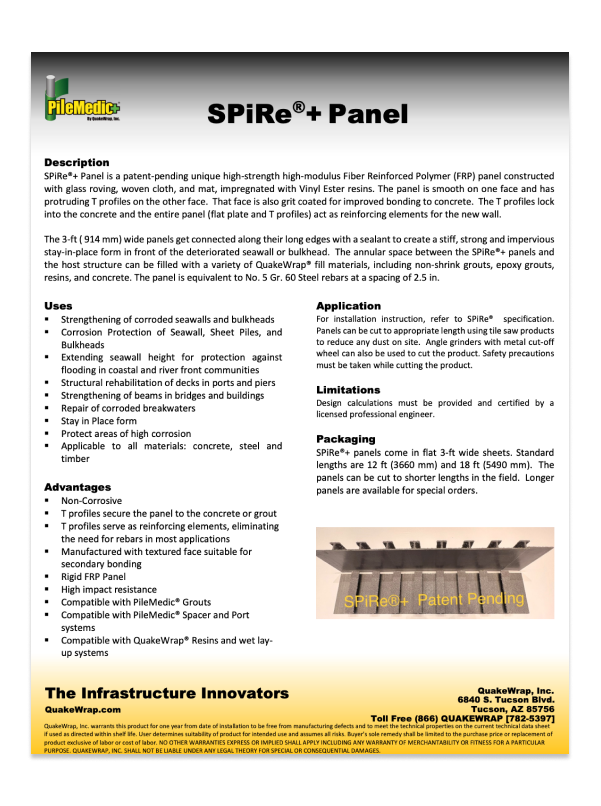
SPiRe+ Product Brochure
Looking for Help with your Project?
Schedule a Call
Get free advice for any upcoming projects or repairs
See Specs and Sample Designs
Get full specs and details to plan out your next project
Frequently Asked Questions
Potential environmental impacts of seawall repair include the disruption of natural habitats, alteration of water flow patterns, and disturbance to marine ecosystems. Careful planning and implementation of repair methods are necessary to minimize these impacts and preserve the ecological balance.
The costs of seawall repair can vary depending on the specific issues and extent of damage, but it is generally more cost-effective than seawall replacement. Professional assessment is key in determining the most suitable option.
Regulations and permits for seawall repair vary depending on location and jurisdiction. It is important to consult with local authorities and obtain necessary permits to ensure compliance with environmental and construction regulations.
Seawall repair methods, such as polyurethane foams and epoxy injection resins, can be used for other types of marine structures. These methods provide effective solutions for sealing cracks, filling voids, and reinforcing structural integrity in various marine installations.
Alternative methods and materials for seawall repair should be considered to enhance effectiveness and longevity. These may include innovative polymer systems, specialized equipment solutions, and advanced foams or resins that provide leak-sealing, void-filling, and structural reinforcement capabilities.